Metal Framing System Product Cost: Steel vs. Aluminum
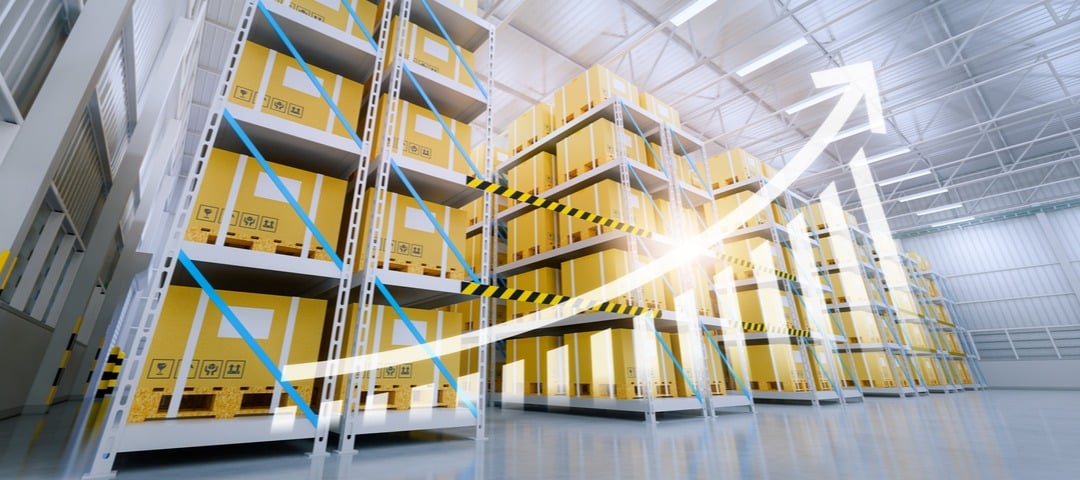
In the industrial world, there’s the daily hustle, and then there’s the bigger picture of operational efficiency.
Both affect revenue at the end of the day, and both are impacted by your material and engineering choices in metal structure design. Choices of aluminum vs. steel, or fastened vs. welded parts, are huge influences on costs both today and way after tomorrow.
Because your metal framing system’s products and processes have such a big impact on the total value of a structure, let’s dive into the nuances of each. The goal is to help you understand which option best aligns with your project requirements and limitations (which aren’t always what they seem).
5 Cost Factors in Metal Framing System Products
There are at least five cost factors that impact the short- or long-term value of aluminum and steel framing systems:
- Turnaround time
- Raw materials
- Labor
- Maintenance
- Modularity
1. Turnaround Time
Ordering a welded frame vs. another style is a wildly different experience. Even going from one aluminum framing system to another can change the delivery date.
Note the difference in process steps between three notable framing types:
Process Step |
Welded Steel |
T-Slot Aluminum |
Self-Aligning Aluminum |
Multiple sources? |
Yes |
No |
No |
Design? |
Yes |
Yes |
Yes |
Assembly? |
Yes |
Yes* |
Yes* |
Surface prep? |
Yes |
No |
No |
Welding? |
Yes |
No |
No |
Annealing? |
Yes |
No |
No |
Machining? |
Yes |
Sometimes |
Rarely |
Squaring? |
Yes |
Yes |
No |
Coating? |
Yes |
No |
No |
As you can see, welding steel (or aluminum, though we don’t recommend it) involves much more than torching a slab of steel. Each step is crucial, but adds to the wait – especially if your manufacturer can’t handle it in-house. It’s common for welding to create a lull of 12 weeks in a project’s timeline.
Think about it: Some places combine multiple operations, but many others are specialists. Thus, each process could involve a different company. Those extra shipping costs matter, along with the additional time wasted moving the product from shop to shop. What if your work cell has to shut down until that critical order is ready?
Even if you employ a welder in-house, there still may be a wait time as they makes theirway through their project list. The more immediate nature of aluminum extrusion building systems is why many cost-conscious designers turn to them.
T-Slot Assembly vs. Self-Aligning System Assembly
*Why the asterisks next to “Assembly” in the chart? There’s a big difference between connecting T-slot assemblies and an equivalent self-aligning frame.
While both systems consist of extruded profiles and various fasteners, assembling a self-aligning aluminum frame requires a much lower labor cost. Because it uses angled fasteners that spring the connection into position, this frame achieves instant precision without having to realign and retighten it several times. You can build an advanced frame in less than 50% the time vs. a T-slot frame.
2. Raw Material Cost
This one’s less about what you have, and more about how you can use it.
But first, the prerequisite statement about raw material price: Historically, aluminum has been more expensive per pound than steel. Market prices can vary based on global supply, demand, and other economic factors.
Anyone wise to material selection knows that’s not the ratio that truly matters. It’s about the materials’ strength relative to weight.
Mild Steel |
Aluminum |
|
Tensile Strength |
~55,000 psi (~380 MPa) |
37,700 psi (~260MPa) |
Density |
(~7.87 g/cm3) (~491 lb/ft3) |
(~2.71 g/cm3) (~169 lb/ft3) |
Strength-Weight |
~47 |
100 |
Aluminum extrusions can hold weight better than you might think. Because aluminum is nearly 3x lighter, the strength-to-weight ratio of extrusion framing is more than 2x that of steel.
Lighter weight means that you can get more strength per pound vs. steel. Combined with smart engineering, this can offset the higher per-pound cost.
Where traditional aluminum “structural” framing (T-slot extrusions, strut channel, tube-and-joint) falters is that they often require extra supports to match the sturdiness of a weldment. This is especially true if the application will involve dynamic forces, and those extra supports undercut any material savings you might’ve had.
For heavy-duty applications, advanced T-slot successors remedy this by creating stiff connections that help profiles retain their strength (rather than each connection creating a weakness). These self-aligning systems don’t need extra cross-bracing, re-establishing aluminum as a cost-effective material option.
Weight can also impact the cost of readying the assembly for use. A heavier object may take extra workers or equipment to set up, adjust, or transport.
3. Skilled Labor
Welding takes talent and time, even on easy-to-work-with materials. There’s a difference between “a guy who can weld” and a true professional welder.
Beyond all the human labor involved in prepping the material, there are also monster truck-sized CNCs and other machines at work. They’re squaring the assembly up, putting it through the painting station, drying it, and so on.
This is why many industrial outfits (especially smaller companies) don’t keep a welder on-hand. It’s an expensive skill to keep in your back pocket, let alone its secondary operations.
Cost of operation is one area where aluminum modular framing has a clear advantage:
- Assembly requires as little as one hex key and minimal skill
- Mistakes aren’t as costly
- Self-aligning connections don’t require fiddling with levelness or alignment
Tip: Remember how a self-aligning aluminum frame is a much faster build than a T-slot equivalent? They’re also easy enough to align that just one person can do it in short order, further reducing labor costs.
4. Maintenance
There are several ways material choice can influence the maintenance cost of structural steel and aluminum framing:
Realignment
Realignment and retightening are the #1 reason light-structural products like T-slots (aka 80/20 aluminum) are cost-prohibitive in dynamic environments like a vibratory feeder. If an extrusion structure relies on friction and pinned connections for support, Maintenance will have to resquare it at least monthly to keep components in place. This monthly investment won’t end until you scrap the structure or replace it with a more rigid alternative.
Those alternatives would be, of course, steel weldments and self-aligning aluminum, whose stiff, clearance-free connections prevent rattling and loosening. Use these systems, and you’ll never tighten a fastener on that machine again.
Fatigue
Fatigue prevention is another source of maintenance, and it’s one that always favors steel. Aluminum has only about ½ the fatigue strength of steel on average. Steel’s more prone to fatigue around the weld area, where heat treatment makes the joint more brittle, but overall it’s still superior to aluminum’s properties.
If your application will involve lots of repetitive movement (like a robotic assembly arm), steel framing may save money long-term. That doesn’t mean you should consider aluminum cost-prohibitive – you’ll just need to design around the limitation. Your aluminum extrusion manufacturer can slow fatigue failure by offering rounded component edges and reinforcing features at potential failure points.
Corrosion
You probably don’t need a reminder that aluminum is more naturally corrosion-resistant than steel. What you may not know is that even a painted, powder-coated, or galvanized steel frame is still more susceptible to corrosion than an anodized aluminum frame.
At minimal charge, extrusion frame makers can artificially anodize the aluminum parts pre-assembly. This spurs the material to form a protective oxide layer on its surface when exposed to the elements. There’s little to no maintenance cost involved with this finish (in most environmental conditions). That sure beats paying for paint and a painter every year.
5. Modularity
This feels a bit like cheating, as steel weldments aren’t really a “modular” metal framing system or product.
With welding you lose functionality and take on additional costs. If you want to add or adjust any elements, that’s only possible by welding again. You’ll have to pay for labor and materials, to the point of stripping the paint because the new weld won’t attach to it.
There’s little extra cost to customizing aluminum extrusion frames. The effort is the same as initial assembly – slide on or off any parts you want to add or subtract, and tighten as needed. This is still achievable with one simple tool and modest skill level. Again, choosing an advanced (self-aligning) system vs. simple T-slots will further reduce your labor investment.
… And the Winning Metal Framing System Product Is:
If you air-drop them into identical industrial situations, an aluminum framing system will usually equal or surpass structural steel framing in cost efficiency.
Ultimately, your total cost of ownership will depend on the production process and your application:
- If you lack a turnkey welding option, several 2-3 week delays might stack up as the product moves from shop to shop.
- Vibration-prone T-slots introduce a recurring maintenance cost that doesn’t exist with rigid-connection systems.
- If your structure must be light on its feet – either literally or in adaptability, aluminum is a labor- and material-conscious way to get there.
If you’re considering the middle ground of modular aluminum with steel-like stiffness, learn more about the AngleLock self-aligning system here:
Leave a Comment