True Strength: T-Slot & Other Aluminum Framing vs. Welded Steel
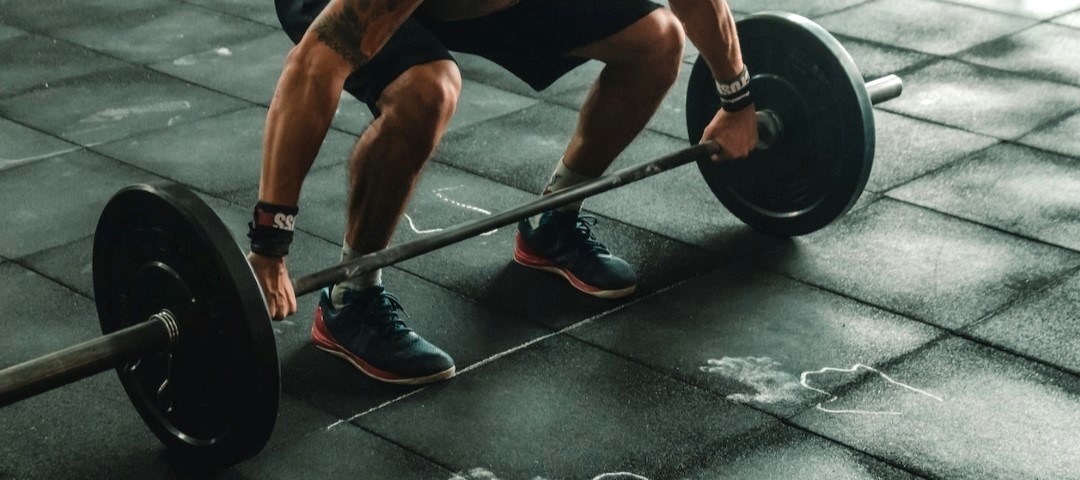
There’s strength in numbers for structural framing systems. In the design phase, material and engineering specs always sound exciting and doable, right?
Or maybe it’s the opposite for you.
Maybe you design conservatively, reinforcing everything and avoiding alternative solutions you’ve heard horror stories about.
At the center is the idea of strength – both in raw materials and how engineering puts them to use. Yet, for being a concept so central to manufacturing, strength is not defined or understood the same way from person to person. This goes for the strength of T-slot aluminum, welded steel, and other “hybrid” framing solutions in between.
Let’s end that by laying out exactly how aluminum, steel, extruding, and welding impact the sturdiness of your final assembly:
- Component strength
- Why distinguishing strength from stiffness is important
- When you’re under- or overengineering for strength
- Fatigue strength
Component Strength: T-Slot Aluminum vs. Steel
“Aluminum is weak” might be the biggest myth in heavy-duty machine and equipment design.
What product do people most associate with aluminum? Soda cans. (Or pop cans, if you’re on the East or West Coast.)
Even experienced and clever engineers can fall for old perceptions – and miss out on design improvements. There are vast differences in strength between an alloy for aluminum canning and one used in framing profiles.
It’s true that steel always wins in terms of pure force. Even standard mild steel profiles have more tensile strength than the 6005 aluminum used in most T-slot and advanced extrusion profiles.
Standard Mild Steel |
Aluminum Extrusions |
|
Tensile Strength |
~55,000 psi |
37,700 psi |
Density |
~7.87 g/cm3 |
~2.71 g/cm3 |
Strength-Weight |
~47 |
100 |
But because aluminum is far lighter, the strength-to-weight ratio of aluminum extrusion framing is more than 2x that of steel. While extrusion brackets are usually made of a different grade (6061), the story’s the same – a well-engineered aluminum system can thrive in industrial environments.
Remember that there are “layers” to strength. From the outside, the concept has always seemed to favor steel. Having peeled back the first layer – strength/weight ratio – we can start to clear up the confusion. Now, on to the next layer to unravel.
You Might Need Stiffness More Than Strength
High-strength materials are a huge performance booster in many industrial applications. However, in many aluminum and steel structure designs, a rigid alignment is more important.
Aluminum has plenty of tensile strength per pound to support most light-to-moderate structural duty. But some engineers mix the ideas of strength and stiffness together, and that’s where problems can begin.
Part of the issue is that connection strength can reduce component strength – and overall assembly strength. In the aluminum framing industry, this is a huge reason why advanced T--slot alternatives exist.
But first, an example seemingly as old as time:
Example #1: T-Slot 40x40 Connection vs. 2" Tube Steel
Close your eyes and think of a simple, cube-shaped machine base. You may have visualized a web of bolted T-slot profiles, each 40x40 mm. Or maybe it was a series of 2” welded steel tube parts.
If you’re picturing these side-by-side, that means you’re comparing pinned- and fixed-connection systems. In dynamic applications, it’s not much of a competition.
Note that your joining method creates strength and stiffness implications for your application. Building a welded base, then an equivalent T-slot base, is the clearest way to see this.
40x40 mm T-Slotted Profile |
||
Measurement System |
SAE |
Metric |
Moment of Inertia |
Ix = 0.024 in4 |
Ix = 13.787 cm4 |
Iy = 0.024 in4 |
Iy = 13.787 cm4 |
In aluminum extrusion framing, wall thickness isn’t a spec that’s considered. What you’re really comparing is its moment of inertia compared to a ⅛” or ¼” thick steel profile. This correlates to stiffness in the cross-sectional area of the selected beam.
In anything but the least-demanding industrial applications, T-slot aluminum framing loosens long before welded steel framing. T-slots use pinned connections, which leave clearance at the joint and cannot resist rotation (aka moments). Welding, of course, produces a fixed (rigid) connection, resisting rotation in dynamic situations.
This is what makes traditional T-slot framing inadequate as a true structural framing system – stability is impossible without support bracing and frequent retightening. Even then, it’s only a matter of time before the fasteners rattle loose again and become a structural-failure risk.
Then there’s the strength impact. An assembly is only as strong as its connections. Because T-slot extrusion fasteners rely on friction at a single plane of contact to resist loads, they inherently sap some of the strength of the connected profiles. Think of it as fueling a luxury sports car with cheap gas.
With steel framing, welding causes no such problems – in fact, it can strengthen the joint’s surrounding area.
Example #2: Self-Aligning 40x40 T-Connection vs. 2" Tube Steel
Why bother with another example? Because here’s where the third layer comes into play: Not all aluminum extrusion systems use pinned connections.
In your comparison daydream (or perhaps nightmare, depending on your application), swap the T-slot cube for one built with self-aligning aluminum framing.
This extrusion system looks similar to T-slots, but is an advanced alternative for structures that require stiffness. The secret is no secret (it’s right in the name) – the assembly “snaps” back into precise alignment whenever something moves it. This is possible through, yes, high-strength brackets, but also – more importantly – fixed, stiff connections. The highly engineered system uses angled fasteners to create several planes of mechanical locking per joint.
Do you see where this might start to sound like welded steel?
40x40 mm Heavy-Duty Profile for Self-Aligning System |
||
Measurement System |
SAE |
Metric |
Moment of Inertia |
Ix=0.343 in4 |
Ix=14.268 cm4 |
Iy=0.343 in4 |
Iy=14.268 cm4 |
The 2” tube steel will be stronger than self-aligning aluminum, but the stiffness will be comparable for most applications. Note that the 40x40 mm aluminum profiles are 0.5 in. smaller in width and height.
Both fixed-connection systems can maintain tight and precisely aligned connection, even during:
- Vibration
- Cyclic loading
- Movement
And because a self-aligning system loses no profile strength from poor connections, the strength of an extruded assembly can rival a welded one.
Is Welding an Aluminum Frame a Good Idea?Nope. There are many methods of joining aluminum extrusions, but for structural builds, welding shouldn’t be one of them. Welding aluminum (extruded or other) causes it to anneal, mitigating some of its heat treatment benefits. When welding aluminum, its anodized protective coating contaminates the weld. The anodizing should be removed from the surface for an effective weld. Mild steel takes the heat (and resulting cooling) better than its nonferrous rival, gaining slight strength and hardness boosts in the affected zone. This is a good thing for most applications, but harder also means more brittle, which makes the weld area more prone to fatigue. If structural rigidity is a priority for your project, but you still want low weight and high modularity, choose a self-aligning system over welded aluminum.
|
Underengineering & Overengineering for Strength
Look around enough industrial facilities, and you’ll see a lot of both issues. Both can reduce the cost-effectiveness of your structural framing system.
Underengineering
This is the more obvious issue to spot, and it’s almost always a T-slot frame that’s to blame.
T-slots get by on crude engineering to provide modest structural support for non-dynamic applications. Where engineers get into trouble is specifying them for jobs they were never really meant to perform. To spot structural engineering flaws, simply watch how a T-slot assembly performs. For example:
- Are safety doors sagging?
- Is a maintenance guy coming in monthly to tighten 200 bolts on the production line?
- Are misaligned sensors causing quality issues?
These are surefire signs that your T-slot assembly isn’t meeting requirements for rigidity or strength.
Overengineering
There’s a flipside, and shockingly, it might actually be more common: overengineering. Factories are a breeding ground for this; many structures and machines are overengineered 3-4x to give the perception of safety.
Do you really need all that strength and stiffness?
Students sign up for karate classes, in part, because they want to grow stronger. But before they learn a single technique, Rule #1 from the instructor is: Practice restraint. You don’t get to go around kicking people in the face just because you’re powerful now.
Much like martial arts require restraint, structural framing requires a right-place-right-time mentality. Overengineering lets you be sloppier in execution, but sloppy is wasteful:
- Adds weight to product
- Assembly is longer and more difficult
- Extra supports obstruct access and become an eyesore
Instead, examine your specs and find the materials and engineering methods that give you “just enough,” saving assembly, material, and other costs.
Aluminum users take note: Self-aligning systems make this easy in that all connections start at 100% strength (because the joints mechanically lock). With the outcomes of your connections predictable, you can mix and match standard- and heavy-duty profiles throughout the assembly. Add strength where you need it, and rest easy about everything else holding up!
Fatigue Resistance
The fatigue strength of steel vs. aluminum framing is a much more direct comparison. It’s simply a matter of material traits; engineering only comes into play as you develop workarounds.
Aluminum has only 50% the fatigue resistance that steel offers. You have to be much more aware of this property when designing with aluminum.
If you grab a paper clip and bend it back and forth, it’ll get continually weaker until it eventually snaps. The same concept applies to any industrial application with cyclic movement.
A robot on the production line may look real smooth as it glides left and right, performing its repetitive task. But even a tough metal component can crack after 1 million cycles.
Unfortunately, once cracking starts, it can propagate in as little as a few minutes. Fatigue life follows an exponential trend – just like a snowball rolling downhill. It may take tens of thousands of cycles to create a crack, but once a crack forms, it quickly grows and fractures. And because it’s on a microscopic level, you won’t notice it until it’s too late.
If your structural build will face an unusually high level of exposure to fatigue loading, steel framing may be your best choice. In most industrial cases, your fatigue specs won’t disqualify you from using aluminum – you’ll just need to design around the limitation.
There are several steps your aluminum extrusion manufacturer can take to slow fatigue failure:
- Round the profile and bracket edges to eliminate stress risers
- Use FEA (finite element analysis) to identify potential failure points, then reinforce those areas
More Beyond-the-Numbers Insight on Frame Systems
Rather than obsessing over the numbers, sometimes the path to design enlightenment is to revisit the core concepts (and misconceptions).
You may perceive the strength of aluminum as being insufficient due to its lower stiffness when compared to steel. Or that aluminum’s strength-to-weight ratio always makes it perfect for machine building.
To avoid under- or overcooking your creation, separate and evaluate the material and engineering implications on both of these properties.
- T-slot aluminum is strong enough for static applications that require a lightweight or low-cost solution.
- Welded steel is for meeting extreme needs in rigidity or another mechanical property.
- Self-aligning aluminum is for combining the perks of weldments (strength, stiffness) & extrusions (lightness, modularity).
Our resource hub has lots more on structural systems – from how to build a metal frame without welding, to additional debates on materials. Explore the resources by clicking below:
Leave a Comment