Aluminum Frame Design – Differences From Welded Steel Framing
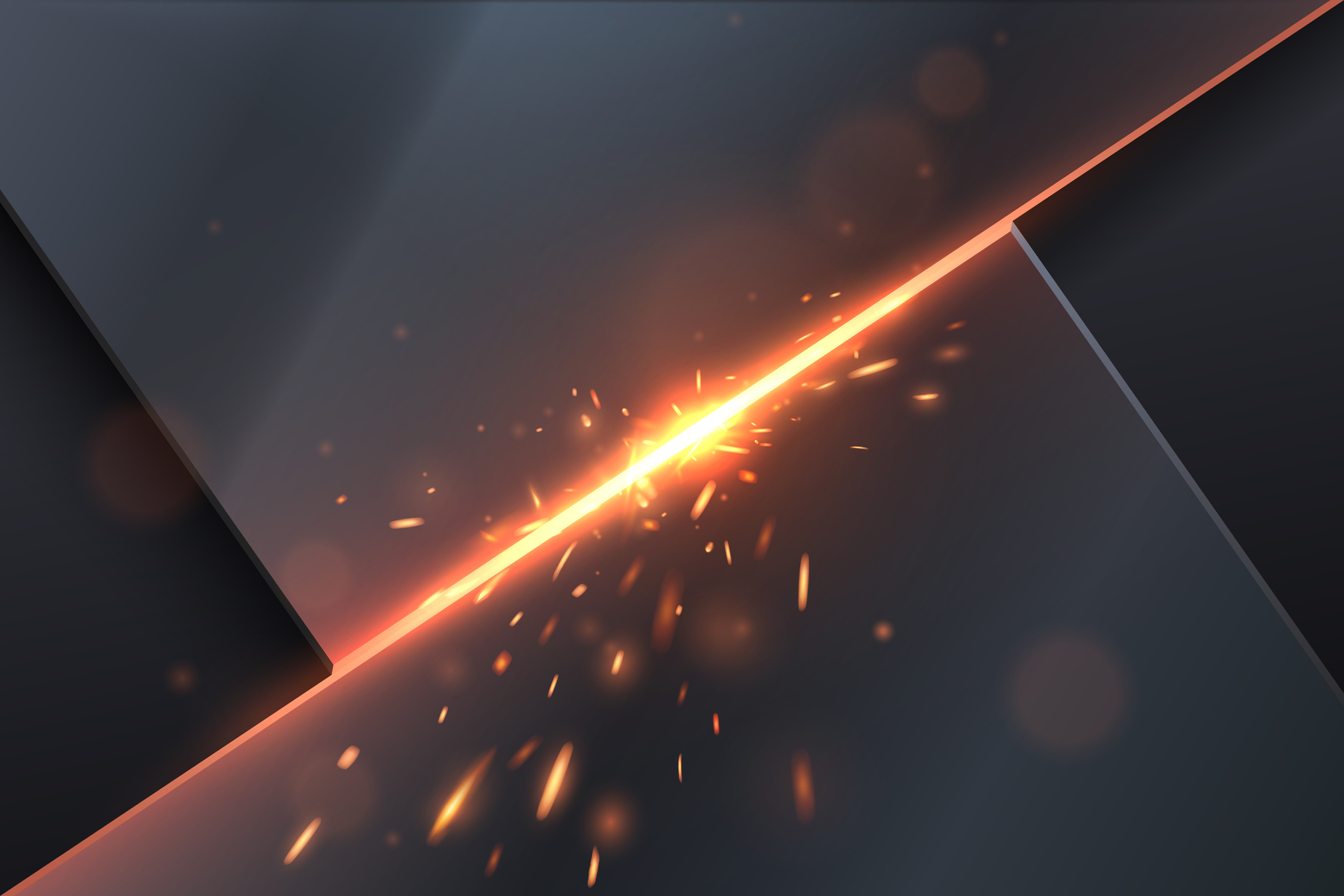
You’re desperate to limit downtime and uphold safety standards with any metal framework supporting your industrial, manufacturing, or automation equipment.
So perhaps you’ve already compared the guidelines of steel and aluminum frame designs, and understand the obvious tradeoffs. But beyond weight-to-strength ratio (though worth revisiting too), what else impacts the long-term success of your application?
6 Design Considerations of Steel vs. Aluminum Frame Design
While welded steel structures remain the front-runner for heavy-duty framing (think buildings), aluminum extrusion has exploded for all other applications. Today, many manufacturers and buyers use aluminum for small bases, guarding, workstations, and more.
The big selling point is that, pound per pound, aluminum is actually stronger than steel. But in a structural framing system, those are just two of several design guidelines to consider:
- Weight
- Strength
- Durability
- Predictability
- Profile versatility & manufacturability
- Assembly
1. Weight
Broadly speaking, aluminum is ⅓ the weight of steel.
The heaviness of an aluminum profile also depends on its alloy and shape. Fortunately, aluminum framing systems rely on extruded profiles, which are usually lighter (and stronger) than rolled or cast ones.
Typical densities you’ll find include:
- Aluminum extrusion: 2.71 g/cm3
- Mild steel: 7.87 g/cm3
If your design will require a lot of components and material, aluminum will probably offer more production per pound.
2. Strength
There’s a reason you don’t see aluminum towers dotting the Manhattan skyline. Steel’s sheer strength carries a better reputation than aluminum with structural engineers.
Many (but not all) common structural aluminum grades offer 30,000-40,000 psi yield strength. A structural steel grade typically comes in around 50,000 psi.
However, you shouldn’t simply go by raw numbers – the equation changes when you consider material weight. Aluminum frames with the same weight as steel ones can provide up to 2x the strength.
This could influence your design choices in two directions:
- Skimp on the amount of material (weight-wise) without sacrificing structural stability
- Employ more material without worrying about excessive weight
Just like with aluminum vs. steel, you must look beyond raw strength when comparing one aluminum grade vs. another. In some structures, the primary design limitation is deflection rather than strength, making modulus of elasticity the #1 factor in performance under stress. Nearly the whole spectrum of aluminum alloys has a similar modulus (about ⅓ that of steel’s). Note that stiffness and deflection are proportional to thickness cubed, so aluminum frames with the same weight as steel can provide 3x the stiffness.
Strength of Advanced Aluminum Extrusions
(Mini-sections by this name will cover design pros/cons exclusive to advanced extrusion systems, which are functionally different from T-slots.)
If a profile’s pure strength has limited impact on some structures’ performance, what does matter? The connection.
A steel joint is generally stronger than the material around it. In standard aluminum extrusions, the joint is the weak point. However, AngleLock’s advanced connection system draws strength from its mechanically locking brackets. Like a steel joint, it’s also stronger than the material around it.
This method uses:
- Angled bolts
- Heavy-duty & adjustable brackets
- Project-specific solutions – i.e. solid rivets, threaded inserts, & custom screws
All are made of 7075-T6 grade aluminum, which offers astounding strength (83,000 psi tensile, 73,000 yield). The self-aligning connections allow the frame to use the full strength of its profiles.
What’s the biggest external threat to your product? If your framing system requires pure strength and can live with subpar corrosion resistance (i.e. indoors), welded steel should work. In the most demanding dynamic applications with potential for corrosion, an advanced aluminum connection system is safer.
3. Building for Durability
Make sure you check off all the boxes here – there are multiple definitions of “durability” in engineering.
Will your framing components play nicely with other elements of your operation? Will they reside in a harsh environment?
Sadly, self-aligning brackets don’t exist in standard T-slot aluminum extrusions. One of the top disadvantages of traditional aluminum T-slot extrusions is the inevitable loosening and misalignment.
When comparing durability from a dynamic, wear-and-tear standpoint, welded steel’s a clear winner for most abrasive applications. T-slots can’t match steel’s superior fatigue resistance, and they lack the stiffness to stand up to all the jostling.
While steel is initially more durable, it can warp and weaken in humid, marine, and other corrosive environments. Unfortunately, it’s pretty much a must that you paint or galvanize welded steel before use.
Aluminum offers superior corrosion resistance thanks to its natural oxide layer. If corrosion would threaten the integrity of your design, and an otherwise weak metal grade would suffice, consider 1100 aluminum. This grade doesn’t provide the best strength or hardness, but does offer good corrosion resistance and thermal conductivity.
One final positive for T-slots: By nature, aluminum releases fewer particles into the air, especially compared to steel that is rusted or otherwise corroded. This makes aluminum less harmful to the working environment. If your design will go in an application where cleanliness is king – such as a sensitive machine enclosure – aluminum is the superior choice.
Durability of Advanced Aluminum Extrusions
Today, extrusion framing technology allows you to combine the stiffness of a weld with the corrosion-fighting qualities of aluminum.
AngleLock modular framing works around the lack of aluminum’s stiffness by using mechanically locking connectors. The fasteners actually tighten over time with vibration, making them a no-brainer over T-slotted systems in dynamic applications.
4. Predictability
If your application is low-risk, you can probably skate by safely with the cheaper (T-slot) solution. Anything beyond that, and you’ll struggle to forecast the behavior of your structural system.
In framing assemblies, a finite element analysis (FEA) helps project the properties and structural integrity of your assembly’s design and materials. Steel weldments are compatible with FEAs, although you still have to make assumptions about the weld’s quality. Weld beads can vary greatly depending on:
- The welder
- Machine settings
- Material uniformity
Unfortunately, there are even more variables at play with standard extrusion frames – an effective FEA of a T-slot system is virtually impossible.
And of course, in dynamic applications traditional aluminum extrusion frames are as unpredictable as they get. Steel is a more reliable source of support for heavy-duty jobs that require years-long stability.
Predictability of Advanced Aluminum Extrusions
Advanced aluminum-based systems open the possibility of FEAs, allowing you to forecast outcomes even more reliably than with steel systems. (Self-aligning aluminum frame connectors are 99.99% uniform from case to case, whereas each steel weld is a little different.)
How does AngleLock framing enable FEAs and predictable outcomes? The connections lock (unlike T-slots, which pivot), and are empirically proven to be as stiff as a weld. This allows you to treat extrusion frames like welded structures when you plan their functionality.
And as you now know, AngleLock’s framing components never come loose – unless you want them to. Can’t get more predictable than that.
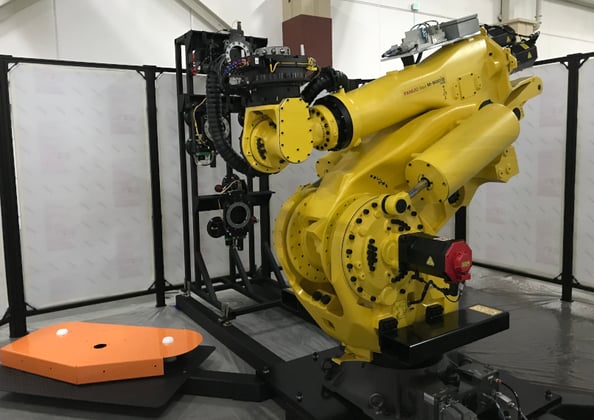
5. Profile Versatility & Manufacturability
If your desired design is off the beaten path, aluminum may better satisfy your creative needs. Simple and standard designs are where steel excels.
Fabricating softer metals such as aluminum is more manageable for two reasons: malleability and lower weight. Steel is hard and brittle, making it a double-edged sword – strong, but difficult to work with.
Your structural framing manufacturer can more efficiently form and bend aluminum into intricate shapes. What’s more, T-slot extrusions also come prefabricated in hundreds of sizes and geometries.
If you prefer a welded structural system, set aside more time for careful planning. Every mount, measurement, and mistake is magnified. It’s tough to reverse course on a weldment-heavy design once it’s complete (for reasons you’ll see in #6).
A unique or intricate shape almost always requires some level of extra effort, and therefore labor cost and lead time, from the fabricator. If your needs are highly custom, take your material’s workability and formability into consideration – aluminum profiles may cause less hassle for the fabricator.
A few other important points that may influence your decisions:
- Thinner wall sections are possible with aluminum vs. steel thanks to its superior strength-weight ratio. If you’re looking to reduce weight or material, start here.
- Smaller aluminum profiles include narrower slots because their stress load is lower and they need smaller connectors. To give you an idea of typical extrusion configurations, a profile may have a 6, 8, or 10 mm T-slot on each side.
Manufacturability of Advanced Aluminum Extrusions
This is the one area where a designer may struggle pushing the envelope with newer aluminum extrusion technology. While the huge classic T-slot library makes for easy sourcing, modern alternatives are limited in variety (though threaded inserts and pivot brackets do add versatility). Self-aligning systems simply haven’t been around as long.
6. Assembly
Who on your team has the skill and time to turn parts into products? Do you have an assembly crew that can place heavy steel pieces, and a welder with the talent to fuse them?
If your design has to be out the door quickly, you may not want to wait for the inherent downtime of steel frame welding. Not only does it take time to weld, but there’s also built-in delay for surface prep, post-weld cleanup, and painting.
If you need an assembly process simple enough to handle in-house with your current crew, aluminum extrusion framing is the solution.
T-slot aluminum profiles are easy for a single worker to connect to nearly anything thanks to their use of simple “T-nuts” and bolts. The system’s much snappier (literally) than working with individual steel pieces that require welding.
Now, what about disassembling or modifying your structural framing – is this important to your design?
Are you confident you’ll get it right the first time? Could your facility repurpose it later?
As your needs evolve, you can adjust an extrusion framing system without restarting at square one. Since you can snap profiles on to closed ends via fasteners, it’s easy to add or remove:
- Doors, sliders, and latches
- Cable management
- Guarding
Because steel structural shapes require welds and precise drilling, welded-steel construction is tough to modify post-build – so plan accordingly. Such an assembly may not be able to adapt if you need to, say, move the structure to a new warehouse.
Modifications and repairs often require outside services to come to your plant. This adds labor and travel costs, as well as weeks of potential downtime waiting for an opening in the service provider’s schedule.
Note that you’ll frequently have to realign traditional T-slots to maintain precision … but, hey, at least it’s an option.
Assembly of Advanced Aluminum Extrusions
Choosing AngleLock framing vs. T-slot systems means another layer of efficiency and value.
This newer structural framing assembly is far the fastest and easiest to set up. Tighten a few bolts on the self-aligning brackets and you’re done. No need to break out a square and make sure everything’s level.
While AngleLock framing connections are as stiff as a weld, they remain adjustable for modifications just like T-slots. Where these systems differ from standard T-slots is that you can unbuild and rebuild them with instant precision.
Steel or Aluminum Frame Design?
Both structural steel and extruded aluminum can provide reliable framing systems. Your unique specs and environmental considerations should determine what’s a fair tradeoff.
- Strength-weight ratio: Steel is still ideal for static stress loads where the weight of the structure isn’t an issue. For products that must be heavy duty but not heavy, self-aligning aluminum systems can create powerful connections.
- Durability: T-slot aluminum reduces corrosion, steel fights fatigue with stiffness, and self-aligning aluminum systems do both – for similar initial cost but reduced long-term downtime.
- Predictability: In high-risk designs, stick to framing systems that offer FEA use and reliable outcomes, like steel weldments and AngleLock.
- Profile versatility: Aluminum is easier to manipulate into complex, thin shapes, plus there are hundreds of premade T-slot profiles on the market.
- Assembly: Modular T-slots are adjustable on the fly, while modern aluminum alternatives go a step further by making it easy to maintain precision during reassembly.
To summarize: Your design may need the sturdiness and predictability of steel, or the shape and assembly versatility of T-slots. But if you need it all, and aren’t under pressure to cut corners on up-front cost, go with self-aligning aluminum tech.
Interested in recent breakthroughs in aluminum extrusion framing design? Check out similar articles on our blog:
Leave a Comment