[PROJECT SPOTLIGHT] Floor Locks for Carts: A Docking Alternative
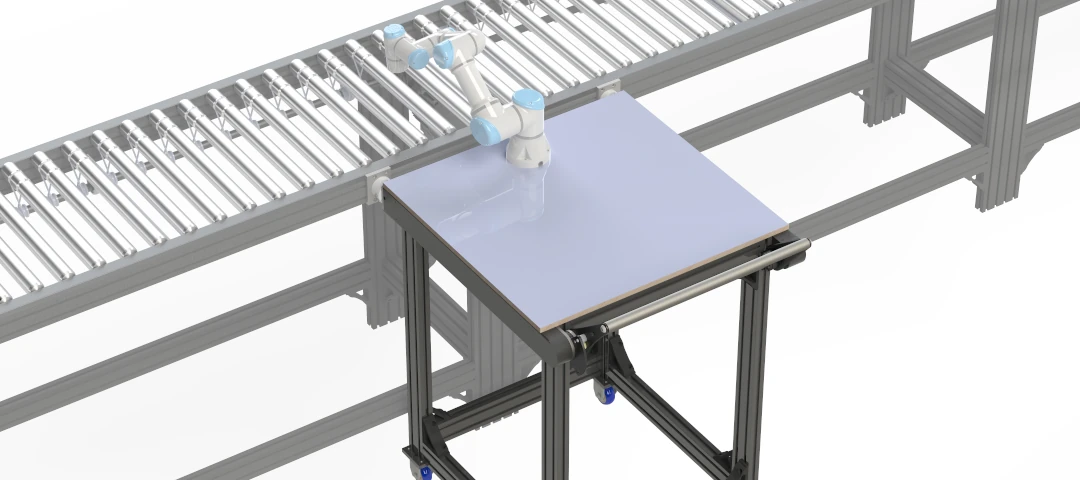
Mobile carts, racks, and stands are a key part of the material handling and automation process. Other than being mobile, they don’t add much to the efficiency and safety needs of those industries.
But what if they did?
This edition of Project Spotlight will show off technology that allows for repeatable docking and removal of industrial equipment. Today’s specific use case will be a more reliable alternative to floor locks for keeping carts, mobile racking, and other wheeled equipment in place.
A video is also below so you can see just how precise a system can be with unique fastening and mechanical locking.
The Problem With Today's Floor Locks for Carts
Efficiency is everything to robotics and material handling applications. A foundational concept of that efficiency is mobility – industrial carts on wheels, robots on rotating stands, and so on.
But that movement must be trustworthy. In this use case, the challenge was finding a better way to prevent movement when it’s not needed.
Current solutions for docking robots and other wheeled equipment include:
- Standard floor locks – On carts, these locks are mounted between swivel casters or diagonal corners. The user steps on a spring-loaded lever, which forces a rubber foot to make contact with the ground. This creates just enough friction to keep the cart in place.
- Locking floor guide – This less-common option works similarly to tracking for a sliding door. Affixing the system directly to the ground creates a secure docking location for the equipment. However, 1” thick steel track makes for quite the dangerous tripping hazard, and you’d have to dig up the whole guide if you need to adjust its location
- Caster-mounted brakes – There are several types based on wheel dimensions and industry-specific requirements. The brake may press on the wheel’s tread, the wheel’s side, or the floor itself to prevent movement. Many of these are a hassle to engage and/or disengage as well as not always providing the most secure brake.
None of these is the most precise solution for setting up an automation line.
Quality of connection is a concern when it relies on friction as a stopper. The system’s integrity erodes over long-term use, and its initial strength isn’t remarkable either. If a structure needs to be in a precise location for automation equipment or sensors to detect and interact with, an inadequate solution could produce defects and logistical inefficiencies.
There are additional concerns around safety, depending on the use case. Racking on an uneven floor could become a runaway train that hurts people or expensive machinery. Safety sensors that are out of alignment could leave potential hazards undetected.
The Solution: Ditch the ‘Floor’ & Improve the ‘Lock’
When a worker needs to move and secure an expensive or heavy-duty object for the factory floor, a standard solution won’t do.
Our #1 recommendation? A mechanically locking docking station for industrial carts.
In the video (starting at the 1:55 mark), a user demonstrates undocking and redocking a mobile robot cart onto a production line. It’s a prime example of taking aluminum extrusion framing and turning it into more than the sum of its parts.
The cart docks and undocks smoothly every time, maintaining precision laterally within 0.003”. Any small vertical inaccuracies in the readings shown are due to shop floor debris affecting the cart's wheels.
This dependability changes the game for operational efficiency in several ways:
Quality Control
While the station looks like a typical extrusion structure, it actually uses the AngleLock framing system, an advanced successor to T-slots that self-aligns during movement. This system uses high-strength brackets and angled screws to create a mechanical lock.
The operator can smoothly and quickly move both pieces of equipment repeatedly while maintaining extreme tolerances. It’s a no-maintenance and high-precision way to lock a rack, cart, or stand onto a conveyor, bench, or anything else to which you can mount receivers.
Safety
Docking systems that can shift or detach while in use are a threat to people and pricey equipment. Thanks to AngleLock’s mechanically locking docking system, unintentional detachment is physically impossible.
Because these connections on the cart and the docking structure itself are built with self-aligning engineering, they don’t loosen with vibration or become a structural-failure risk. And bringing the concept from the floor directly to the connecting equipment means there’s no tripping hazard.
Flexibility
Assembly, movement, and adjustment of an AngleLock cart-docking station is easier and faster than clumsy T-slot and burdensome steel alternatives:
- Connecting parts slide on with instant precision
- Assembly is 50% faster than with T-slots
- Parts are lightweight and fewer in total
You can take this self-aligning system wherever you need it in the facility. There’s no need to dig through concrete to uninstall it.
We’ve found one possible, minor drawback to using AngleLock as an alternative to cart floor locks. Pushing a heavy load into a connection that’s not anchored to the floor could cause the line equipment to shift slightly. That said, the reference point will still be spot-on because once the cart locks in, it becomes one piece with the line.
Industries & Uses
Rigid, reliable support is welcome in many industries and processes. Self-aligning aluminum systems offer that, at a competitive total cost of ownership, because the connections can go decades without maintenance or replacement.
As you watch the operator in the video reattach the robot cart to the workstation seamlessly, perhaps your mental wheels are turning with your own ideas.
Meanwhile, here are a few more of our suggestions:
- When a sensor has a reference point your mobile equipment must be at
- For a “blind” robotic manufacturing tool that doesn’t use a vision sensor, so it relies on exact part location
- Moving heavy components to an optical inspection station
(Note: Certain equipment needs to be built from an AngleLock frame to successfully attach to AngleLock docking. For example, if you use our cart-docking system with a cart made of 80/20 framing, it will warp over time and lose its precision..)
More Than Just a Floor Lock for Carts
You probably won’t have trouble coming up with your own application for this industrial metal cart dock. It’s a very useful tool that solves for:
- Repeatable accuracy
- User & machine health
- Operational speed
We’re excited to hear what you come up with. If you want a better understanding of self-aligning aluminum framing (in particularly, what sets it apart from T-slots), check out this page:
Leave a Comment