Fixed- vs. Pinned-Connection Structural Metal Framing Systems
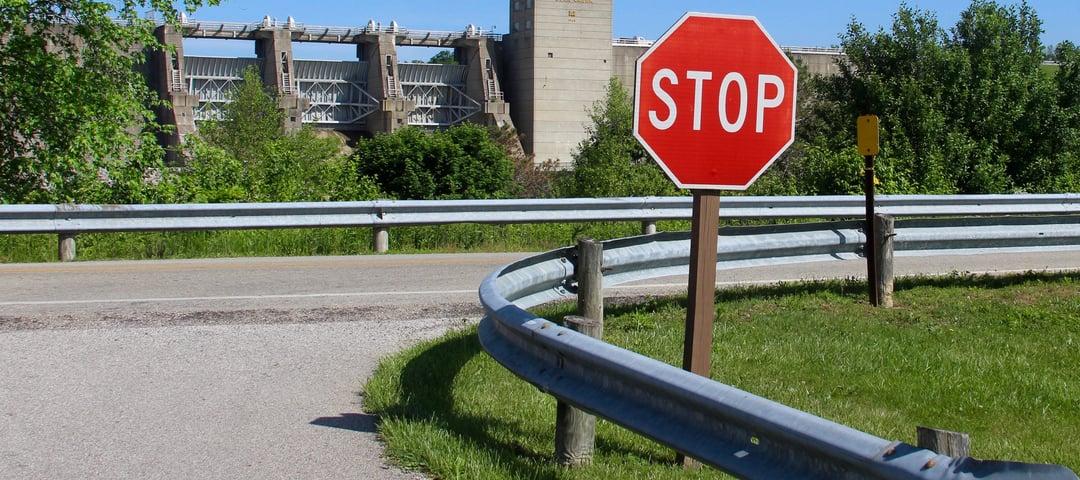
In structural systems, connections play a pivotal role in overall strength and stability. There are many ways the engineering world categorizes these connections and the various types of structural framing systems.
If you use structural framing as a building system (for machines and equipment, not skyscrapers) there are only two categories you need to know. In metal framing, those are fixed connections and pinned connections.
A close examination shows some surprising truths about both aluminum and steel structural framing systems.
Pinned Connection
A proper pinned connection stops structural members from translating or slipping, but does allow them to rotate. There are two sights common with pinned framing – a lot of clearance at the bracket and the ability to rotate, even after tightening.
Pinned modular systems may be connected with bracing to resist lateral loads (drifting).
Examples
There are many types of metal framing systems and components with pinned connections, so we’ll stick to common examples:
T-slot aluminum extrusion framing relies on pivoting and friction to keep components together. It relies on cross-bracing to provide lateral stability.
Tube and joint framing, like T-slot, is not very structural. Its main appeals are lightness, appearance, and diversity of shapes and sizes.
Door hinges are an obvious everyday example – you literally drop in a pin.
Advantages
- Parts and labor are typically lower-cost up front.
- Rotation at the connection point can accommodate slight deformations from load or temperature change. In some projects, engineers prefer the flexibility of a pinned connection.
- Installation and replacement is simple compared to some fixed-connection options. T-slot and tube components snap on and off easily, making the systems mistake- and modification-friendly.
Disadvantages
There’s intentional movement, and then there’s unintentional movement. How much you desire (or can tolerate) in your modular build will determine whether pinned systems are worth the fight:
- While pinned structural components won’t shift up and down or side to side, they can’t create a moment-resistant frame. Twisting forces at connection points will cause deflections in vertical loads and more potential for structural failure. T-slot connections also translate a bit due to the clearance in the holes. You can brace a pinned connection to get it to behave like a fixed one, but it still won’t quite perform to those standards.
- These systems’ long-term value is poor because of the unavoidable downtime they come with. In T-slots’ case, your team will lose many hours per year to retightening and realigning the system. It also takes 2x as long to assemble a T-slot structure than an equivalent design that uses certain fixed connections (more below).
- T-slots and other pinned-connection assemblies may require additional bracing to prevent unwanted rotation. The extra parts drive up material and assembly costs, reduce operator access, and complicate the alignment process vs. more robust framing connections.
Fixed Connection
Rigid frames use fixed connections to provide extra stability in at least one direction. These structural members neither rotate nor translate.
Fixed, rigid connections are a part of any moment-resisting frame system. And they're as structural as it gets.
Examples
Tougher to find, there are a few notable types of metal framing systems with rigid, fixed connections.
Weldments are permanent connections created by fusing two pieces together. Mild steel is easier to weld than stainless steel, and holds up to the process better than aluminum.
Self-aligning aluminum framing uses extruded profiles, just like T-slots, but puts a 180° spin on the engineering behind them. Angled bolts and five planes of contact help lock the joint in all directions.
Concrete moment frames are set in a fixed connection by default. They sometimes include holes to reduce resistance to accidental impact. Specific examples include deck patios, I-beams set in concrete walls, and traffic signs.
Advantages
- Fixed connections prevent moments, creating a stiffer structure for high-vibration applications. They don’t require additional bracing to prevent unwanted rotation, keeping sensors and other critical components in accurate alignment.
- They remove the possibility of fatigue caused by relying on friction and pivot points. The superior load distribution adds long-term stability and safety.
- Aluminum fixed supports offer competitive flexibility vs. pinned supports. Even though the connection is rigid, the softness of the material provides enough elasticity to survive impact stress.
- The reduced need for support pieces equals efficiency across the board. It streamlines material cost, aesthetic clutter, and operator accessibility. Self-aligning extrusion building systems to reduce bracket count by an average of 25% to 50% compared to a similar T-slot structure.
Disadvantages
The sore spots of using fixed joints vs. pinned joints are generally confined to the widely known limitations of welded framing systems.
- Rigid steel frames are more likely to shear because they lack the flexibility to endure slipping out of alignment. If a heavy cart bumps into a welded steel conveyor, there’s no shock absorption to save your production line.
- Welded frames are more difficult and time-consuming to install and replace than pinned connections. You’ll have to wait for a skilled technician to be available – hopefully you have one on staff already.
- The up-front purchase may be pricier than that of a tube or T-slot structural framing system. Welding is expensive, while self-aligning systems include high-strength brackets priced to match their durability.
Going Structural? Use a Fixed-Connection Frame
Pinned connections are best for modular framing systems that’ll experience minimal stress. Fixed connections were born to stand tall against moments, vibrations, and deformation.
While pinned connections score points for stress flexibility and (sometimes) ease of use, they rarely belong in industrial-grade builds where safety and maintenance time matter. And while fixed connections almost always win vs. pinned, you probably noticed welded and self-aligning systems have their own pros and cons based on:
- Toughness in heavy-duty environments
- Ease of assembly & modding
- Total cost of ownership
To see a quick example of a fixed connection improving an aluminum framing design, check out this PDF:
Leave a Comment