Combating Aluminum Fatigue Failure in Your Framing Design
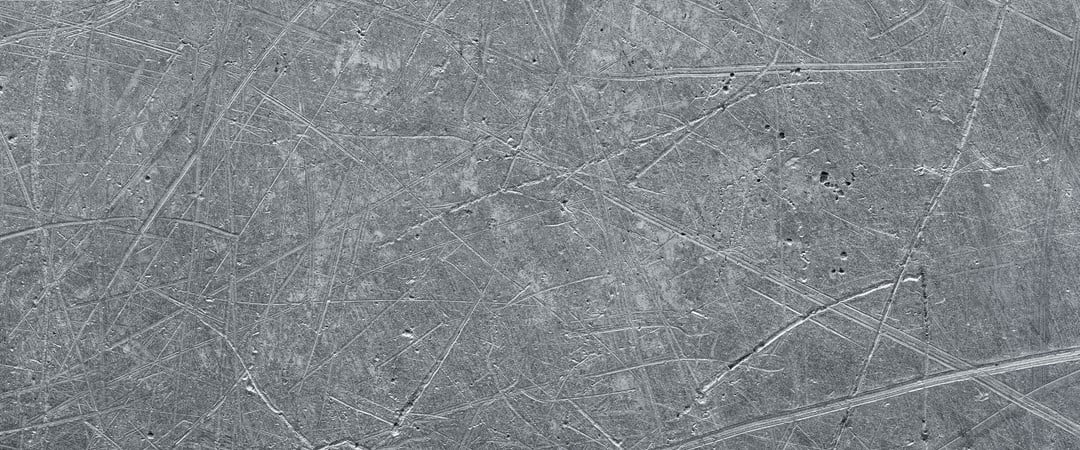
If it’s good enough for the aerospace industry, shouldn’t it be good enough for you?
We’re, of course, talking about aluminum. You love it for its lightweight and corrosion-resistant properties. You shake your fist at it when fatigue failure occurs.
Nobody understands the benefits and limitations of aluminum better than aircraft engineers and others involved with the design of mission-critical framework. With no choice but to use lightweight materials, they’ve managed to build reliable aluminum structures through advanced connection technology and clever workarounds.
There’s good news: You can adapt the same strategies for machine bases, automated material-handling lines, display booth setups, and other aluminum applications.
First, let’s identify the warning signs of aluminum fatigue failure in a framing system. Then we’ll point out six key strategies for working around the problem and maximizing the value of modular structural aluminum.
Defining Aluminum Fatigue Failure in a Framing System
Did your spouse hang one of those tacky “Live, Laugh, Love” knickknacks on the kitchen wall? In the world of load-bearing design, the saying might go “Life, Limit, Loss.”
Even in non-construction applications, aluminum that’s reached its fatigue limit is a safety and quality threat.
Fatigue failure in aluminum occurs when a material cracks under repeated stress that’s below the material’s ultimate tensile strength.
Causes include:
- Cyclic loading
- Stress concentrations
- Environmental conditions
Most often, these cracks start at “stress concentrators” like:
- Holes
- Sharp corners
- Notches
One symbol of the fatigue life of an aluminum part is an S-N (stress-number of cycles) curve. This measurement describes the relationship between stress amplitude and number of cycles to failure.
However you look at it, don’t underestimate the impact of extending aluminum’s fatigue life when designing light and moderate structural systems.
6 Aluminum Fatigue Failure Tips Any Industry Can Use
Take some cues from the aerospace industry and address these six factors in aluminum frame fatigue:
- Sharp edges
- Joining method
- Material properties
- Stress distribution
- Treatment
- Maintenance
1. Avoid Sharp Edges
Even on extruded brackets, fatigue is a surprisingly common issue.
Sharp corners |
➡️ |
Stress risers |
➡️ |
Fatigue |
Traditional T-slot corners are sharp and crack easily, creating issues of both structural and user safety.
The solution, this time, is simple: Avoid sharp bend radii in corners and notches. Use components with smooth transitions and rounded corners to distribute stress more evenly. This reduces both the starting and spreading of cracks.
If you’re up for investing in a system that’s a bit sturdier than T-slots, consider self-aligning aluminum framing. This rigid connection system uses profiles and brackets with rounded edges to make aluminum more competitive with steel welded framing.
2. Joining Method Affects Rigidness
Connection type |
➡️ |
Level of rigidity |
➡️ |
Fatigue rate |
One of the many ways the type of metal connection system affects performance is fatigue.
Movement creates fatigue in a metal frame, just like it does in a human being. We’ll once again cite our favorite analogy on the matter: bending a paper clip. If you continuously bend it a little bit at a slow rate, it’ll reach its breaking point slowly. If you continuously bend it back and forth much farther and at a high speed, it’ll snap quickly.
Depending on the bracketry and extra bracing you include, a more rigid build may move less and thus experience less fatigue stress. In T-slots, cross-bracing is an acceptable solution in low-impact operations.
If you need a higher level of vibratory stress relief in your aluminum design, self-aligning framing is the answer. This system uses angled fasteners and high-strength brackets to mimic the rigidness of steel, never coming loose in high-movement applications.
There’s also, of course, the welding route you’d typically see in steel frames. If you join aluminum this way, the weld spots will be more susceptible to fatigue. That’s because stress looks for the path of least resistance, potentially prodding the material to start cracking. This is one of the reasons welding aluminum framing isn’t an ideal solution (along with its difficulty and expense).
If you insist on welding, enlist a tradesperson with aluminum-specific knowledge of how to avoid cracks, pores, and inclusions. Techniques such as friction stir welding might offer superior fatigue resistance vs. conventional methods.
3. Material Properties
Aluminum’s fatigue properties are only about 50% as good as steel, assuming you’re looking at “typical” versions of each material. But you’re probably here because you really, really want the lightness or corrosion resistance of aluminum in your application, right?
You have options.
Just like fatigue strength varies from metal to metal, it varies to a (lesser, but still notable) degree among individual grades.
Choose aluminum alloys with higher fatigue resistance, such as alloys in the 2XXX, 6XXX, or 7XXX series.
Examples of Fatigue-Resistant Aluminum
Grade |
Fatigue Strength |
Strong Enough For … |
6061 |
Good |
Structural profiles on heavy-duty vehicles, bridges |
2014 |
Very good |
Aerospace framework |
2024 |
Great |
Sheet form for aircraft wings & fuselage |
7050 |
Amazing |
Aircraft fuselage frames, bulkheads, and wing skins (heavy plate applications) |
7075 |
Amazing |
Aerospace components, rec equipment (bikes, rock climbing) |
You can figure out the fatigue strength of an aluminum alloy by dividing its tensile strength by 3.
Remember, not every part on a framing assembly needs to be Superman. Select a fatigue strength level based on the component’s loading conditions.
4. Check Your Stress Distribution
Have you designed for minimum stress concentrations? Distribute loads evenly across the structure through intelligent design.
Features like fillets and curves at critical stress points can reduce the likelihood of new and spreading cracks. Where stress concentration is unavoidable, you can try applying fatigue-resistant materials and coatings. Extra bracing that restricts movement at the joint can also limit the effect of fatigue. Sometimes a slight increase in material costs or design complexity can greatly extend service life, offering better long-term value.
A finite element analysis (FEA) is a smart path to optimizing the design before, rather than after, you open the box. FEA software can simulate load conditions and identify potential areas of stress concentration.
Self-aligning aluminum framing’s predictable connections work well with FEAs; the shaky nature of T-slot systems make them less compatible with FEAs.
5. Treat It Right
The harder a profile’s or bracket’s surface is, the more prone it is to stress risers that cause cracking. On top of that, some 80/20-style T-slot brackets are cast, which makes for a rough and at-risk surface.
A smooth surface finish can significantly improve fatigue life because they seal potential crack initiation sites. Processes that improve surface quality and fatigue performance include:
- Anodizing
- Polishing
- Coating
Heat treatment is a similar deal.
Component stress-relieving processes clean up the mess left by machining, cold working, or grinding. More specifically, the appropriate solution heat treatment, quenching, or aging process can re-establish your desired fatigue strength (and improve other properties).
6. Play the Maintenance Detective
Certain parts of a framing assembly are more prone to fatigue. Make sure you know what they are ahead of time.
When structural fatigue takes off, it really takes off. By the time you notice it, it’s probably too late to save the structure. The best way to handle fatigue is to not let it happen in the first place.
Part of putting that in practice is following tips #1-4 above. You can also try routine inspection techniques for the early detection of cracks.
Historically it’s been tough to monitor load control with one’s own two eyes without the help of a strain gauge. However, there are non-destructive tests that can identify surface and subsurface cracks:
- Ultrasonic testing
- Radiography
- Dye penetrant inspection
There are other steps you can take to further protect an important structure:
- Lubrication: Reduces friction and wear in moving parts
- Recoating: Reinforces protection against corrosion and wear
- Scheduled replacement: Removes fatigue-prone parts after a certain number of cycles, even if fatigue isn’t visibly obvious
Presumably, if you’re designing something with serious fatigue risk, you’re doing enough analysis beforehand to prevent a worst-case scenario. If you’re building a robot frame, failure probably won’t be catastrophic. If your project is an airplane wing, allowing it to fall off at 20,000 ft. altitude is bad for business. The sensitivity of the project determines how much time you should invest in ongoing analysis.
Aluminum’s Failure History Is an Opportunity, Not an Obstacle
In the universe of modular aluminum framing, addressing the challenge of fatigue is not just about prolonging what you paid for. It's also about ensuring safety and performance in the industries that rely on it most. Through strategic design, an application-appropriate maintenance plan, and the right material system, you can make aluminum structural fatigue a minor inconvenience rather than a roadblock.
As you push against the notion that aluminum isn’t “heavy-duty,” you’ll find opportunities to innovate your framing-based designs, just like aerospace engineers have done. Stay adaptable and informed, and you’ll get the most out of your aluminum structures – whether underground or miles above land.
Leave a Comment