Guide to Fastener Torque Specifications for Modular Framing
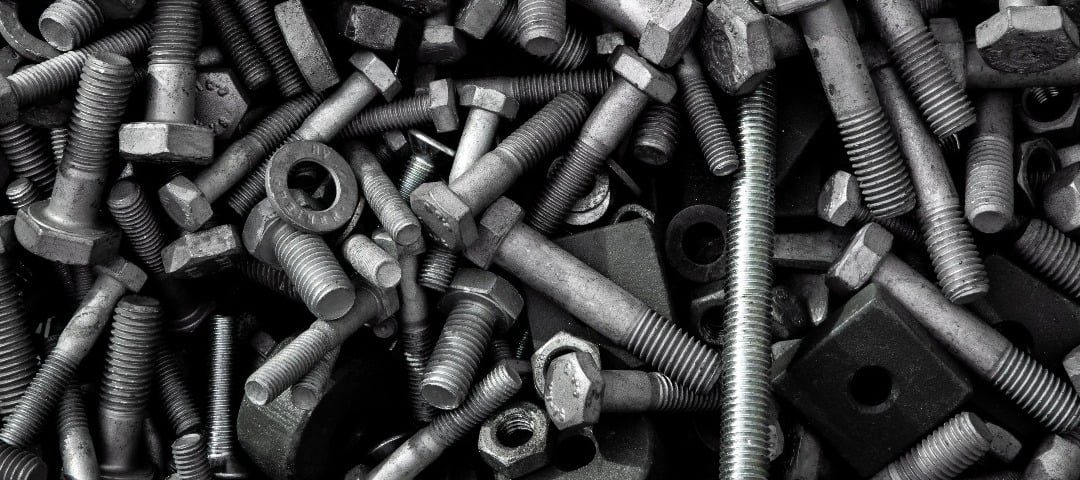
Pop quiz: What’s the one spec nobody seems to understand in structural framing?
Torque.
“Nobody” is an exaggeration, but even established customers often lack a full grasp of fastener torque specifications.
When you’re working with a modular aluminum framing system, a small adjustment in hardware can really tighten up your structure’s quality.
Let’s review torque: the importance of it, how a fastener’s grade and size affect it, and how your framing system can work better because of it.
The Importance of Fastener Torque Specifications
Using the appropriate bolt or screw torque is key to performance. Several factors can influence screw tightening torque standard:
- Fastener size
- Material type (of both the fastener itself and the items being fastened)
- Thread type
- Environment (temperature, humidity, etc.)
Higher torque equals higher clamp load, which increases friction. It’s like trying to yank a tablecloth out from under Thanksgiving dinner vs. doing so with a nearly bare table.
If connections don’t have enough clamp load in a structural frame, profiles will be more likely to slide around over time. In practice, this misalignment can cause industrial sensors to not function or door frames to sag.
If you overtorque a bolt – especially with an aluminum system – there’s a good chance the head or nut will sink into the profile like mud. This creates a stress riser, which decreases the fatigue strength of the profile.
Bolt Size vs. Grade in Torque Rating
As you probably know, there’s a variety of grades of bolts. Maybe you’re less familiar with the way a fastener’s grade affects torque rating.
The perception of a larger bolt is, “It’s bigger and therefore must be stronger.” This isn’t always correct.
An M8 bolt is stronger than an M6 bolt, but minimally so. The increase is 5-10% – it’s not a 25% jump like some folks might think.
Bolt Type |
Metric Grade |
Imperial Grade |
Highest-grade |
12.9 |
No direct equal |
High-grade |
10.9 |
8 |
Standard-grade |
9.8 |
5+ |
Low-grade |
8.8 |
5 |
A bolt’s strength rating carries some weight too. T-slot extrusion manufacturers tend to promote their use of M8 screws and bolts, yet they’re often rated 10.9 or lower. High-grade bolts tend to be 12.9 or higher, and they’re available in M6 size.
This is why advanced framing for dynamic applications uses smaller, higher-grade bolts (along with fixed, self-aligning connections). An M6 rated at 12.9 and an M8 rated at 10.9 are a lot closer in strength than you’d think. And every little reduction in assembly weight and footprint is welcome.
Matching Your Framing System to the Hardware
A structural framing system should be designed to match the hardware you’ll use to fasten them. And vice versa.
What does that mean in practice? Don’t let the perception of strong hardware obscure the reality of your spec requirements.
Calculating Bolt LoadThe equation for bolt load based on applied torque is T = KFd.
Surface coating and operations can impact these friction traits. |
- In many T-slot framing systems the hardware is far stronger than the brackets. Depending on your perspective, the system is either seriously overengineered or underengineered. Because the brackets fail comparatively quickly, they don’t use the full strength of those oversized bolts.
- An advanced, self-aligning system treats joints as a whole – two pieces of rail, the bracket, and the fasteners. The manufacturer designs each element to last about the same amount of time. The system’s engineering is also able to apply more of the hardware’s strength.
Therein lies the benefit to using appropriately sized hardware. A system that fully leverages a bolt’s strength can make it act more like a spring. An example of this is a head bolt in a car that stretches as the metal of the engine block expands with heat. Another example is in self-aligning structural aluminum systems. As a bracket vibrates or is hit with a load, the angled screw will stretch, then pull the bracket into place once the load is gone.
Another advantage of self-aligning extrusion framing is the use of five angled points of contact between M6 fasteners and components. This compounds the previous benefit, creating a stiff, mechanically locking connection you’ll never need to retighten. You could implement an M8 bolt that way, but it’ll struggle to achieve elasticity in the same way.
Torque as a QA Check
There’s a quality-assurance element to torque, too.
- Strength – QA processes often include checking that the torque applied to fasteners meets the specified requirements. This ensures the connections are secure and capable of handling the loads for which you designed them.
- Consistency – By understanding torque specs and keeping them uniform, your production team can tighten every fastener to the same standard. This reduces the likelihood of failure due to under-tightening or over-tightening.
- Durability – Consider your application and verify that your connection system’s torque will stay sufficiently tight when subject to vibration and other forces. Traditional T-slot connections will loosen and lose torque value; self-aligning framing will retain clamp load throughout use.
- Tools – Quality assurance teams use torque wrenches and meters to measure and verify torque. Regular calibration of these tools ensures their accuracy.
Keep Torque Top-of-Mind for the Project’s Lifetime
Size matters … until it doesn’t. Consider the full, detailed picture of screws, bolts, and torque, and how they can affect your structural build.
- Under-torquing an aluminum structural system can result in structural failure and misaligned functional parts. Over-torquing can cause stripped threads and broken fasteners.
- Oversized bolts can be a misleading symbol of strength.
- From a QA standpoint, adhering to initial fastener specs isn’t enough. It’s also about creating trust in the structure’s reliability.
For more tips on designing and assembling industrial and commercial structures, check out our resource blog:
Leave a Comment