Picking Adjustable Angle Brackets for Structural Framing Systems
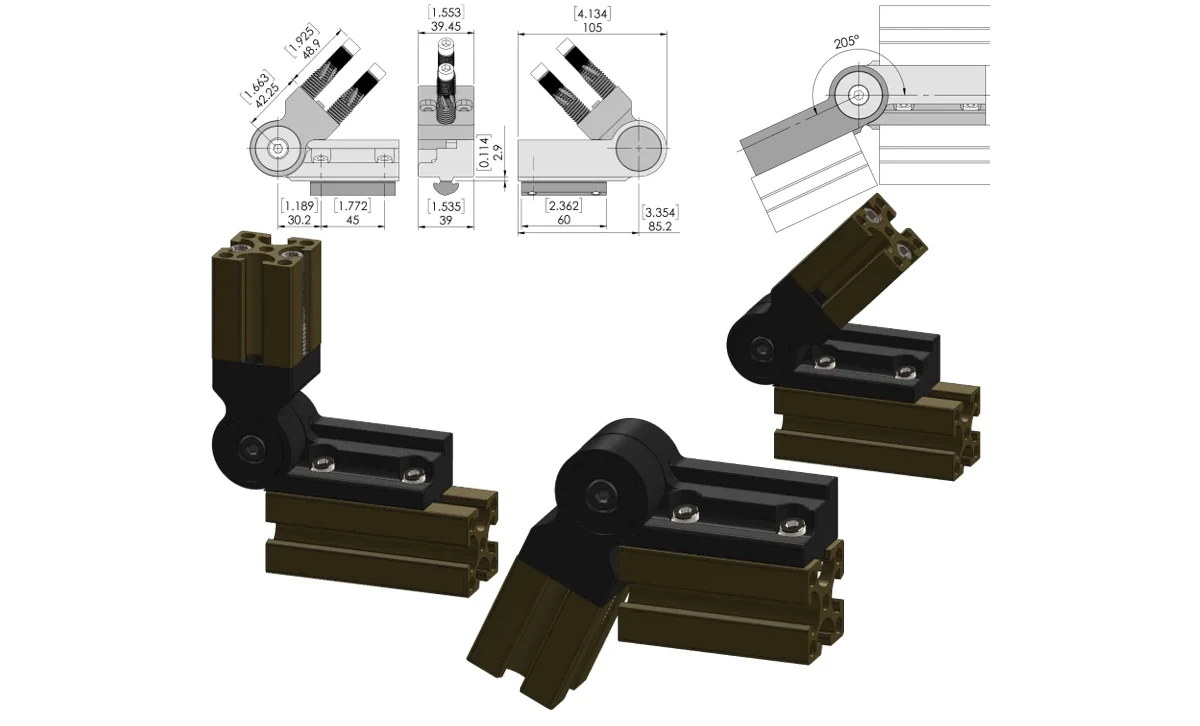
Angle brackets have many names – corner, mounting, L, cleat angle, terminal, gusset, and so on. With some clever engineering, they can add just as many benefits to your structural framing system.
When a standard, fixed-position bracket isn’t enough, a heavy-duty, adjustable angle bracket may have to take over. Popular in braces and supports, highly engineered aluminum brackets are adding new applications – and levels of sturdiness – by the day.
To level up your structural designs, delve into the most important traits of good brackets, no matter what you call them.
What Is an Angle Bracket?
Angle brackets are fastening components that join two pieces of structural framing perpendicularly or at another angle (usually 60°, 45°, or 30°). Used correctly, they strengthen the point of connection and improve the overall assembly.
These brackets are common in robotic bases, machine enclosures, and other manufacturing and automation applications. They come in a variety of shapes, sizes, and materials.
What Makes a Good Adjustable Angle Bracket?
Adjustable angle brackets provide very different results based on the engineering applied and your intended use. To get great results, pick your framing connection components based on:
- Strength
- Enduring precision
- Adjustability
- Aesthetics
- Cost efficiency
1. Strength
Adjustable metal angle brackets can greatly expand the strength of your overall framing system. In particular, the amount of weight that aluminum extrusion framing can hold has come a long way.
For example, adjustable framing brackets using 7075-T6 grade aluminum offer tensile and yield strengths in the 80,000s and 70,000s (psi), respectively. In demanding applications, a good bracket is one that can leverage this high-strength aluminum for:
- Rivets
- Threaded inserts
- Custom screws
Just be warned that standard T-slot aluminum framing doesn’t use these specialized parts and materials. To get their benefits, you’ll need to enlist a high-end extrusion framing manufacturer. High-end (self-aligning) adjustable framing supports carry a slightly lower strength rating than non-adjustable ones, but are still significantly stronger than traditional T-slot brackets.
Another quality to look for in a connection system is adaptability to your strength requirements. You could build a coffee table with welded steel supports, but why bother when wood works fine?
Now apply that thinking to your industrial application. With a customizable line of framing components, you can reserve high-end brackets for critical areas of the assembly. In less-critical areas, you can save money, weight, and space (for accessibility) by using lighter-duty brackets.
At minimum, a good bracketing system offers at least two options (standard-duty and heavy-duty).
2. Enduring Precision
This is the design feature that structural metal support systems mess up the most.
Fortunately, with a little education on new technologies, you can use either aluminum or structural steel angle brackets successfully in a rugged application.
T-slot angle brackets won’t be a good option in environments with vibration or cyclic loading – so get that idea out of your head immediately. Why are T-slot connections poorly suited for dynamic situations? In a word: instability.
Stability is a slightly different trait than strength in that it refers to the ability of a connection to remain in its original position without slipping. The rigidity of your bracket material – and the engineering behind its function – impacts its ability to remain bonded over the years.
A traditional T-slot bracket with a big hole and small bolt must be manually aligned and relies on friction to hold position. One good bump and the bracket moves to a new position, causing misalignment.
This is why so many designers trust welded steel – it offers a permanent connection. Plus, the hard nature of steel offers superior impact resistance.
How About Automatic Precision?
There is one way to achieve the stiffness of a weld when building with aluminum extrusions – but you’ll need very specific brackets.
Self-aligning bracketing systems fasten onto aluminum extrusions, but allow you to far surpass the durability of T-slotted connections. They work internally with the same concept as rivets – a tapered design inserted into a precision hole with no clearance.
Because of this, you can adjust self-aligning brackets to any position at a precise angle. Once you tighten these unique designs onto the rail, they stay secure, even in times of vibration and shock loading.
These premium brackets eliminate the maintenance inherent to T-slot systems and weigh far less than steel angles.
3. Adjustability
We’re talking about adjustable angle brackets, so why wouldn’t we discuss adjustability? The ability to continuously modify your connection allows you to get the best value from your industrial framing.
Brackets for aluminum extrusions should allow you to adjust the angle case-by-case – and that position should hold indefinitely. If you don’t like where it is, you should be able to easily loosen, adjust, and tighten it in a new position.
Modular aluminum framing is the ultimate repurposing tool – it allows you to add, remove, and relocate assemblies. Your corner brackets should do the same, easily snapping onto existing components with a simple tool and minimal skill.
This is where structural steel angle brackets struggle. Welding angles into your system takes a lot of skill (and labor cost). The connection itself may be sturdy, but once it’s on, it’s on – unless you cut it out. Then you have to weld, clean, and coat the connection all over again.
4. Aesthetics
This quality may mean everything or nothing to you, depending on your application.
First off, a good bracket is appropriately sized to your assembly. It’ll simply look better, so make sure the dimensions match your structure.
Bulkiness rears its ugly head on welded steel framing in other ways, too. Because you can’t easily snap components on and off, the assembly becomes a mutated mess as you add pieces over the years.
T-slot connections also have this problem to a lesser extent. Many T-slot extrusion structures feature several diagonal cross-member supports, and the result looks cluttered. If you like aluminum, using self-aligning brackets helps you reduce the number of supports necessary.
Corrosion is another long-term aesthetic concern.
Adjustable aluminum brackets perform well in outdoor and other harsh environments thanks to their natural, protective oxide layer. Steel structural angles will start to rust quickly unless you paint or powder coat them. Even coated parts have limited corrosion protection, and you’ll have to occasionally refinish the components, hampering your cost efficiency (see #5). Galvanized steel narrows the gap in corrosion resistance at an added cost, but still doesn’t perform quite as well as aluminum.
Finally, the ideal angle bracket offers an attractive initial appearance.
Aluminum adjustable brackets are anodized for protection and come in two finishes:
- Clear
- Black
For aesthetically minded projects, a good bracket maintains its Day 1 look for years to come. Aluminum extrusion framing components are easy to clean, while carbon steel connectors are not. Steel does score points for offering an entire spectrum of paint and powder colors, though you’ll lose the metallic look. (You can coat an aluminum bracket too; it’s just not essential to protecting it.)
5. Cost Efficiency
Above all else, a worthy angle bracket adds value to your project – both short- and long-term.
Criteria #1-4 all play into cost. Strength is primarily what you’ll pay for up front. The other three impact total cost of ownership:
- A durable bracket will add years of service life to other components.
- A well-protected bracket reduces maintenance costs due to corrosion.
- A versatile bracket allows you to modify and repurpose – rather than replace – assemblies.
(A customer's original framing design. Note that there are no brackets. The customer drilled holes through the profiles for access, then tapped them in the end of the profiles to thread a bolt. This machining process takes extra time and to either have the distributor do it or use a milling or drilling machine in-house.)
(A redesigned version with AngleLock self-aligning brackets. It uses 50% fewer parts and weighs nearly 1/3 less.)
If you’ve been burned by cheap parts before, consider this example of high-end framing components adding cost-friendliness to an assembly.
Adjustable Angle Brackets – The Engineer’s Role
The right adjustable angle support bracket can improve an industrial assembly’s:
- Strength
- Useful life
- Versatility
- Look
Look at your application. T-slots and their bracketing components will work if you only need modularity and corrosion protection. The properties of structural steel angle sections will work if you only need durability and strength.
If you need some of everything, self-aligning aluminum systems offer mechanically locking, adjustable angle brackets that lower your cost of ownership.
The cube-shaped assembly example was a joint effort between the customer and the supplier’s engineering consultants. Whether you call them adjustable L brackets or cleat angles, talk to your structural framing manufacturer about the best option for connection supports:
Leave a Comment