Angle Bracket Design: Load Stress in Modular Structural Framing
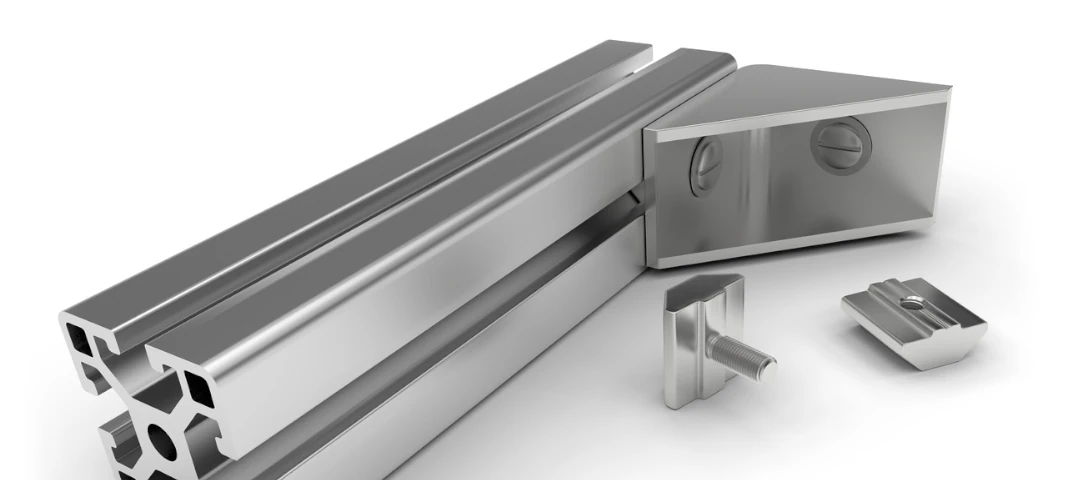
How do you treat your connections – as an afterthought or a feature?
Angle brackets (also called braces or cleats) are common in everything from simple joining tasks to complex industrial machinery. The shapes, sizes, and materials are just as diverse. In modular and structural framing, some components excel at form, some at function, and some at meeting a low dollar figure.
With the right angle bracket design, you can achieve two – or three – of those F’s at once.
If your project is industrial in nature, you’ve probably got load ratings, capacity calculations, and stress analysis swimming in your head. However, both new and revamped assemblies can benefit from stripping priorities back to the basics of a bracket’s engineering. Simple changes in part design can bring major value in time and money.
Sections:
Pinned vs. Fixed Angle Bracket Designs
This is maybe the most obvious place (after a little education) where you’ll notice how advanced bracket designs differ from generic, commodity fasteners.
All angle brackets are L-shaped and join two profiles in an assembly. That doesn’t mean all angle brackets are created equal.
In structural framing systems, the key is in the connection.
Pinned connections stop structural members from translating or slipping, but do allow moments (rotation). The non-rigid connections offer some flexibility and are easy to slide on, but in many industrial applications, they need constant maintenance to remain stable.
Fixed connections are rigid, resisting both translation and rotation. They’re more expensive up-front, but (depending on the specific type) can save material, assembly, and maintenance costs.
You’ll find examples of both in framed structures:
Type |
Fixed or Pinned? |
Rec’d Use (Industrial) |
Note |
Bolts |
Either |
Aluminum |
Potential for strong, adjustable bond. Must consider spacing, bolt size, material, & torque. |
Welding |
Fixed |
Steel |
When profiles can’t be welded, brackets can seamlessly reinforce & join profiles at various angles. Good technique & material are musts. |
Riveting |
Either |
Aluminum |
Structural-grade rivets exist for heavy load bearing. These have higher tensile and shear strength vs. traditional rivets. |
Threaded inserts |
Either |
Aluminum |
Secure fastening using screws or bolts. Consider the insert type, material, compatibility with the frame. |
Adhesives |
Fixed |
Neither |
Non-structural bond. Depending on material and load needs, adhesives may suffice with proper surface prep. |
Selecting the appropriate connection method depends on:
- Presence of vibration or cyclic loading in application
- Load-bearing capacity
- Other desired material properties
- Ability to assemble accurately & quickly
- Potential for modifications
Welded brackets are rigid, with all the impressive mechanical properties of steel. (Don’t weld aluminum; the decreased performance isn’t worth it.)
If aluminum brackets are on your wish list because they’re lighter and more modular, rigidity will depend on the specific system you use. Traditional T-slot extrusions are cheap and readily available, but they’re unreliable structurally due to their “pinned” brackets relying on friction at a single contact point. A newer, premium alternative – self-aligning extrusion framing – uses angled bolts and five planes of contact to create a fixed connection that mimics a weld. This system can be an ideal middle ground when you want to have your cake (stability) and eat it, too (modularity).
Your Brackets’ Footprint
Ideally, you’ll use the fewest brackets possible with the least amount of material possible, right? This is where your angle bracket’s load capacity starts to pay off (if you’ve got it right). Your choice of connection system will influence how much space and money the structure eats up.
It’s easy to over- or underengineer based on misconceptions and default habits. It might sound weird, but both are opportunities to reduce the footprint of your fasteners.
OVERengineered Connection |
UNDERengineered |
Adds weight |
Hamstrings strength of profiles |
Makes assembly harder & more expensive |
Adds routine maintenance to re-square & retighten connections |
Extra supports obstruct access |
Misalignment = more hazards, quality issues, & shutdowns for access |
Welded steel framing parts are nearly 3x heavier than aluminum alternatives, but their strong and rigid connections eliminate the need for extra reinforcement. In a dynamic application, this means they’ll require much less physical space than a T-slot frame, which will need extra bracketing and cross-bracing.
But aluminum extrusions have a superior strength-to-weight ratio and allow easier modification … which would be a shame to miss out on, right? If your build could benefit from aluminum, this might be another opportunity to use advanced, self-aligning brackets instead of T-slot fasteners.
- Example A: Look at a self-aligning, three-way corner bracket. By connecting three profiles to a top plate, this single bracket can make multiple other pieces obsolete. They come with some serious side benefits, too, including consistent precision and easier installation.
- Example B: An equivalent T-slot structure would require a bracket for each of the three profiles, plus two more for mounting the top plate. And it still won’t be as strong as the self-aligning product.
‘Location’ of Bracket Strength
This is a tale of maximizing vs. optimizing the strength of a frame.
We’ve identified that welding makes much better use of space than most other structural connection systems. Like any other system, this is only true if you trust your angle bracket design calculation. Industrial machines and structures, especially ones with steel frames, are often overengineered 3-6x to guarantee safety. Admirable, but often unnecessary.
Each bracket should optimize the strength of its connected component appropriate to its vertical load. Only rigid connections like weldments and self-aligning aluminum can do this; cheaper T-slot brackets inherently cap the strength potential of connected profiles.
Any decent line of brackets offers at least two options (standard-duty and heavy-duty). Rigid bracket design allows you to strategically place high-strength connections at critical points of the assembly and lighter-duty brackets elsewhere to save on:
- Materials
- Weight
- Assembly time
Note: A heavy-duty version of a 40 mm self-aligning corner bracket weighs 1.02 lbs, while the standard-duty version weighs only 0.34.
Your project may also call for an adjustable angle bracket to add another level of versatility. Modularity in general is much more prevalent in extrusion systems than in welded ones; adjusting the latter requires cutting, surface prep, rewelding, and recoating. In aluminum extrusion framing, adjustable brackets allow quick and easy changes at the geometry of your choosing.
Bracket Size
There are plenty of articles on bracket sizing out there, so we’ll stick to the basics:
- Account for all dynamic forces – both inside the assembly and external – that may stress the bracket.
- Calculate the maximum load the bracket will need to support in the worst-case (but realistic) scenario.
- Consider the strength-weight ratio of your material – a bracket using a weaker metal will need to be bigger.
Note: Adding thickness to a bracket can change the bend radius, which in sheet metal brackets may cause clearance issues. However, extrusions don’t have this problem.
Designing for Fatigue Resistance
Fatigue resistance is all about the analysis of the angle bracket’s stress and potential points of failure.
Material
Aluminum has only 50% of the fatigue resistance of steel. You need to be much more aware of this property when designing with aluminum brackets. Aluminum connections tend to be 6061 T6 or 6005A T61 grade, which are similar in fatigue performance.
If your structural build will face an unusually high level of fatigue loading, steel components may be your best choice. But in most industrial cases, your fatigue specs won’t disqualify you from using aluminum – you’ll just need a design workaround.
Shape
Stress concentrations occur at bends, corners, and other geometric oddities. By staying mindful of these areas, you can design your structure to help the brackets distribute stress more evenly, increasing fatigue resistance.
One key to making aluminum feasible in high-fatigue situations is using brackets with a simple tweak in geometry. Self-aligning aluminum brackets are engineered to eliminate sharp corners and other features that create stress concentrations that contribute to fatigue cracks. Most T-slot brackets, unfortunately, keep the sharp edges, creating both a stress risk and an injury hazard.
Corrosion’s Impact
In a corrosive environment, no metal used in structural framing is 100% failsafe. For example, aluminum naturally forms a protective oxide layer over time, but even it can experience 25% or more fatigue in a mildly corrosive atmosphere.
Match your material choice to the level of impact chemicals and moisture may have on your application:
- Steel brackets corrode in anything but the tamest environments. Some steel frame manufacturers galvanize their brackets, while the occasional T-slot system uses steel brackets with zinc plating. These options are better than painting, powder coating, or leaving the steel bare, but are still inferior to aluminum.
- Stainless steel brackets haven’t gotten publicity here because the material is pricey and hard to work with, limiting its use in industrial building systems. However, in specific cases where corrosion resistance and sterility are critical, stainless steel may be worth the investment.
- Aluminum brackets are available in several finishes. Some aluminum brackets are anodized for resistance to water and chemicals, while other extrusion suppliers only powder coat them or leave them bare.
Bolt Type
If you’re going the extrusion route, it’s not challenging to find an angle fastener strong enough for your job. It’s still important to understand the difference between appearances and reality when it comes to fit.
T-Slot Bracket Bolts
Many notable T-slot manufacturers (i.e. 80/20) use an oversized steel M8 bolt. It’s meant to look menacing, but it provides little extra value to your connection.
Because of its size, you have to overtorque the bolt, which distorts the aluminum bracket and profile. The bolt isn't working with the substrate; it’s actually fracturing the surrounding material as you tighten it.
Self-Aligning Bracket Bolts
In the same application, a self-aligning aluminum frame will employ an M6 bolt. It’s the same material, but a different approach to engineering the connection.
A good everyday parallel is the head bolt in your car engine.
The smaller M6 bolt, being lower in strength, becomes more comparable to the strength of the aluminum bracket. This is actually a good thing – it means you’re using the hardware to its recommended limit. This setup has a stretching effect on the steel bolt, improving the resilience of the joint.
Engineering ≥ Material
Revisiting the steps of making an angle bracket has hopefully given you a better understanding of how to specify one for your next frame.
In most applications, the bracket material itself isn’t as important as the way you use it.
Other important factors exist, too, such as connection stability, ease of assembly and disassembly, and total cost of ownership. The effort put into your connections will determine whether they’re a flaw or a feature.
Leave a Comment