[PROJECT SPOTLIGHT] Automated Machinery Enclosure Manufacturing
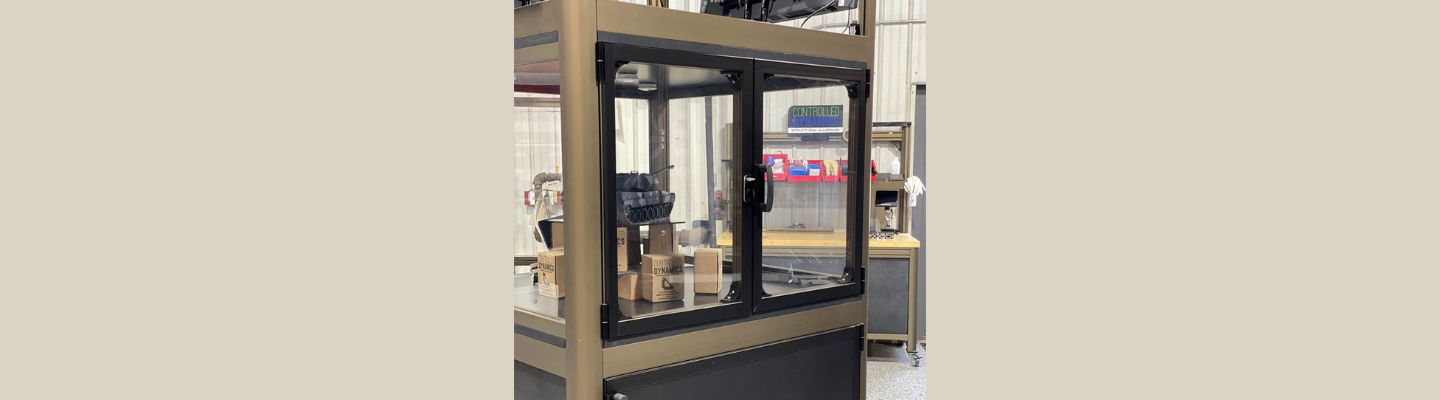
How an Automated Machinery Enclosure Manufacturer Evaluates Your Design
(Rather get straight to the answer to your problems? Skip below to the "Solution" section.)
Above is today's example, an automation enclosure with a parallel-plane plate structure.
Historically, all aluminum electronic enclosure manufacturers have used the same basic T-slot system. This decades-old process uses an oversized fastener tightened to a high torque, with bolts aligned perpendicularly to the profile, to keep components in place.
In today's example, that outdated solution wasn't enough, so an engineering re-evaluation was in order. Here are the criteria your custom cabinet or enclosure manufacturer should evaluate for a project like this:
Strength
Will the application include a high stress load and dynamic movement? Could highly engineered brackets and bolts be worth the investment to improve the assembly's strength?
Except for the most quick-and-dirty jobs, the manufacturer should engineer every enclosure component for maximum precision and performance.
Useful Life
The constant movement of automated applications requires structural support that'll be reliable for years. A supplier should keep longevity in mind when building an automation enclosure -- it should outlive the internal components it's housing.
If the framing system will face vibration or other movement, it may need to pivot away from ... well, pivots. Traditional T-slot framing relies on friction where the bolt hole’s clearance allows the joint to pivot, but this becomes loose and misaligned over time in an automation application.
Buying a replacement enclosure is a headache because of the need to remount and reoptimize components. Furthermore, many factories add enclosures on a wall between existing equipment, making maintenance a hassle and even a safety hazard.
Fortunately, this project used alternate fastening we'll cover further below.
Modularity & Flexibility
A metal formed profile should accommodate other components and be easy to join with other framing elements.
In this project, disassembly was also an area for improvement. Line operators crave lightweight, configurable assemblies. In other words, automated machinery enclosures often call for assemblies users can tear down and move with ease -- without skewing their specs or production speed.
Where Will It Go?
There are several types and uses of automation enclosures:
- Wall-mounted
- Free-standing
- Operator interface
- Console
- Hazardous-location
- More
Solution -- Precise Alignment & Quick Assembly
The structural aluminum framing system in this enclosure is like no other. Its high-precision alignment is why parallel plane structures are possible via aluminum extrusion technology.
The parallel planes in the framing structure allow for mounting robots and linear guides with automation. Mounting is possible on both the top and bottom platens of the enclosure.
The fastening system works by creating bonded surfaces that offer precision alignment. The fasteners create no distortion or stress. They're strong like a welded surface, but the design enables the user to take the structure apart.
(A corner bracket fastened to structural aluminum)
Much of the project's success was impossible with traditional T-slot components. Instead, it uses AngleLock components -- similar in looks to T-slots, but with drastic changes in functionality.
Because of the unique mechanical lock created by AngleLock's fastening system, the enclosure actually tightens over time. It can go years without even minor maintenance.
In the automation industry, benefits of this metal framing solution include:
- Full strength potential -- Engineered for maximum performance (instead of cheap cost), this framing system relies on its brackets to contribute strength. This differs from traditional systems, where the connection is always the weak point.
- Longer service life -- The fastening system never loosens or becomes misaligned, even with heavy vibration or other movement. The decreased need for maintenance practically guarantees a lower cost of ownership.
- Endless possibilities -- The framing system assembles, disassembles, and moves with ease. The user can configure it so effortlessly that customization and repurposing is practically limitless.
Operation: Automation Robot Mount & Docking Cart
- Robot mount: +/-0.0002 in. (5 microns)
- Docking cart: +/-0.003 in. (75 microns)
Adapting Your Own Enclosure Design
In machine enclosure manufacturing, a seemingly simple design miscue can send you back to your 3D model to study what went wrong. So can failure to adapt.
Both issues will slow your automation machinery's short-term production rate and long-term health.
Hopefully the example of the plane-parallel plate structure shows you what's possible with a little creative re-engineering. The project outlasted previous solutions because it relied on AngleLock structural framing components for optimal strength, rigidness, and assembly.
To learn more about the exciting advances keeping the heart of your operation beating strong, click below:
Leave a Comment