Vibratory Bowl Feeder Troubleshooting – A Designer’s Tips
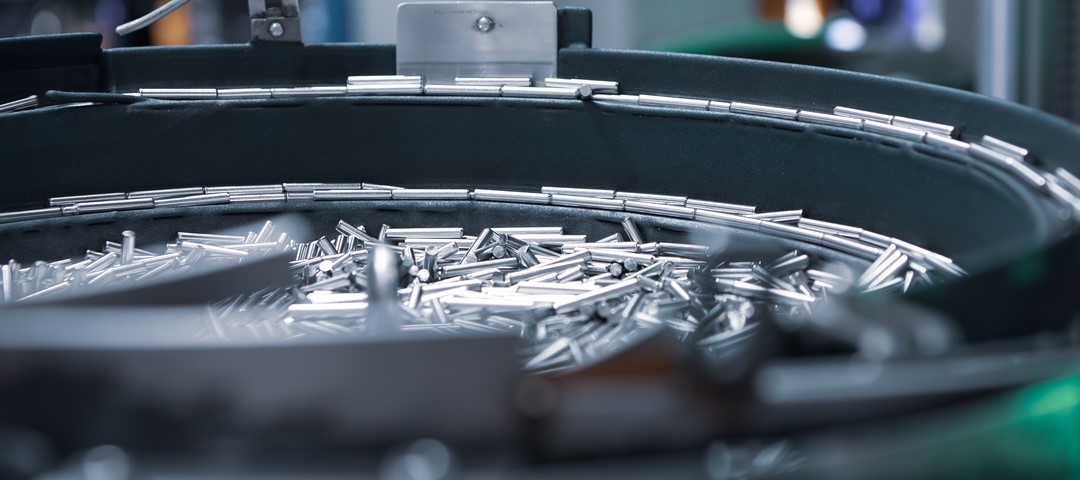
The vibratory bowl feeder is a simple idea that’s turned into a standard for productive, speedy factory automation. However, unexpected bumps in the road such as misalignment, jamming, and inconsistent feed rate can disrupt this surprisingly delicate operation. These disruptions manifest themselves in costly downtime and headaches (perhaps literally, thanks to the noise).
The solution? Approach vibratory bowl feeder troubleshooting with an engineer’s mindset.
This means considering how the structural support and integration of the feeder into the broader system can impact its performance and reliability.
6 Trouble Spots With Vibratory Bowl Feeder Troubleshooting
When optimizing a vibratory feeder bowl for efficiency, these are the top trouble areas to tackle:
- Blaming the bowl vs. the framework
- Clamping isn’t secure
- Dead spots
- Noise
- Interference vibration
- Poor installation
1. Blaming the Bowl vs. the Framework
The process might look helter-skelter, but bowl feeding relies on precise vibrations to move parts to their proper destination. If the feeder is unstable or poorly aligned on its structural frame, inaccuracies and jams may follow.
Here’s the thing: Factory employees often assume poor feed rate is the bowl’s fault, when in reality the framework is to blame. Depending on the framing system used, the mounting plate or the table itself may not be sturdy enough for a dynamic environment. For example, while T-slot aluminum extrusion frames offer a good balance of strength, rigidity, and lightness, not all are created equal.
There are other possible reasons for inaccurate results, like worn components and fluctuations in power supply. However, these issues are more commonly understood and don’t result in blaming the vibratory feeder bowl manufacturer.
Solution #1: Ensure that the structural framing supporting the bowl feeder provides a stable and level platform. Use adjustable feet or mounts on the frame to fine-tune the feeder's position and level it accurately.
Solution #2: Schedule regular alignment checks to identify and correct misfeeding, jams, and uneven wear on the feeder’s components. By routinely verifying the precision of the feeder within its supporting framework, operators can prevent minor issues from escalating into downtime, lagging production, or machine damage.
Solution #3: Use rigid, fixed-connection framing in your assembly to make retightening and realignment a moot point. One example is a welded steel frame, which doesn’t rely on rickety fasteners. If you want to keep aluminum for its lightness and modularity, but don’t trust traditional options, try self-aligning extrusion framing. This advanced system uses angled fasteners and high-strength brackets to mimic the rigidity of steel, maintaining alignment during vibration.
2. Clamps
Clamps can be the source of a couple of issues in a feeder bowl application. They typically happen because:
- Bowl isn’t properly seated in all toe clamps
- Clamps aren’t tight
Either way, the result is slow or irregular vibration.
Much like with tip #1, the culprit may be loose connections in the assembly. The vibration that the process creates needs to go into its intended purpose – moving and orienting parts. Rattling assemblies waste some of that vibration energy by placing it on the support frame.
Solution: Ensure secure connections and alignment of all parts in the assembly. The structural frame’s design should be rigid enough to handle the rigors of vibratory feeding.
3. Dead Spots & Cracks
Sometimes an area of the feeder refuses to cooperate, and it’s not a clamping issue.
- Dead spots: When vibration doesn’t effectively reach certain parts of the bowl, part production can’t flow smoothly.
- Spring fatigue and cracking: The springs that generate vibration lose their effectiveness as they wear, leading to cracking that compromises the consistency of vibration.
- Bowl cracking: Excessive vibration, impact, or material fatigue can upset the flow of parts and create a scary safety hazard.
In these cases, the frame’s rigidity – either too little or too much – could be at fault.
When a frame isn’t stiff enough, vibration dissipates into the frame rather than the parts in the bowl. The bowl will operate less efficiently, and you’ll need to fine-tune it more to accomplish the same results. When a frame is too stiff, vibration can fatigue it, possibly leading to structural failure.
If your feeder bowl isn’t operating exactly as you intend it to, you’re losing energy and money. The ideal conditions are a stiff frame with a stiff mounting – anything less invites unwanted movement.
Remember: Vibration is energy. To create vibration, you need to power something. A vibratory bowl feeder’s cost of operation will be 2x higher if it requires 2x the energy to maintain a normal pace. This is like compensating for poor house insulation by jacking your thermostat up to 82° every day.
Solution #1: Build connections that protect the framework from the impact of bowl vibration. Since T-slots slip out of alignment easily and welded steel frames require special training and equipment to construct, consider self-aligning aluminum framing as a balanced compromise. These fastened extrusion systems mimic the rigidity of steel, but without the expense and lead times of outside fabricating services.
Solution #2: Add mounts that isolate vibration between the feeder and its structural frame.
4. Noise
Naturally, parts production is a noisy operation, but sometimes it crosses the line. Loud machines are:
- Hard to communicate near
- A long-term hearing damage risk
- Unpleasant to work around
If your vibratory bowl feeder design has to spend extra energy to meet your desired production rate, it’s likely going to be louder. Stray vibration transmission to the surrounding structure can compound your noise issues.
Excessive feeder bowl noise could be a framing problem. If you’ve got parts that are loose and vibrating, it’s inevitable that they clack and clang. Think of it like your washing machine’s spin cycle (especially if the load gets poorly distributed).
Solution #1: Adding an enclosure to the operation will mitigate noise levels. A clever enclosure design can make the workspace more pleasant while maintaining easy access for maintenance and monitoring.
Solution #2: Use a connection system that remains tight and in alignment, minimizing vibratory noise. At the same time, see if you can replace overly rigid welded connections that amplify sounds.
Solution #3: Incorporate vibration isolation mounts between the vibratory feeder and its structural frame to minimize the transmission of vibrations. This can reduce noise while boosting performance.
5. Interference Vibration
Subjecting a feeder bowl to multiple vibration sources can result in conflicts of interest – to the point that neither is accomplishing anything. In the worst-case scenario, the combined shaking can create resonant frequency – fatiguing components until they prematurely fail.
The issue may be that the feeder bowl isn’t in correct placement on the assembly. Or, the connected machinery may have stability issues of its own, creating a shaky partnership. An example is a welding robot attached to a machine that orients the hex nuts.
If your operator has to keep punching into the machine every 5 minutes because the feeder bowl isn’t working correctly, it’s time to identify the root cause. Besides the obvious drops in production, you don’t want the risk of a worker constantly jamming a screwdriver in there to dislodge a stuck piece.
Solution #1: Verify that the feeder bowl is in correct placement on the assembly. Ensure the feeder bowl aligns properly with other components or machines, allowing for smooth transfer of parts and preventing bottlenecks or misalignment.
Solution #2: Is there an opportunity to improve the rigidity of the attached machine? Integrating a single, movement-resistant framing solution could bolster the cost-efficiency of the entire process.
6. Improper Installation
Proper installation is the cornerstone of any industrial build. If other troubleshooting turns up nothing, try going back to the machine’s beginnings.
Issues can cascade and sink your productivity when you perform a bad installation:
- Misalignment
- Erratic vibration
- Excessive noise
- Premature wear
There are plenty of paths to a wayward installation:
- Poorly tightened fasteners, allowing vibration to go to the wrong places
- Omitting a component(s) during frame assembly
- Clumsy bowl orientation or leveling
- Poorly configured electrical parts or controls
Solution #1: Touch up the tightness, configuration, and leveling of all relevant structural parts. Verify the inclusion of all components on the supporting framework.
Solution #2: Schedule regular inspections of connections, especially if you use pinned-connection framing like T-slots. Listen and watch for unusual sounds and spastic feeder behavior.
Solution #3: Simplify the structural assembly process by choosing a user-friendly system. Modular systems streamline the process of fixing mistakes and adapting to changing needs, requiring less time, skill, and money than weldments do. Self-aligning aluminum framing takes ease of extrusion assembly even farther by sliding on with instant precision – no resquaring or retightening necessary.
BONUS: Accessibility
Don’t let accessing the machine turn into a troubleshooting event of its own.
Routine maintenance is important to the reliable operation of bowl feeders, especially if your framing system doesn’t perform well in dynamic applications. Poor accessibility can complicate maintenance tasks.
Solution: Design the structural framing to allow easy access to key components of the vibratory bowl feeder for cleaning, adjustment, and part replacement. Modular framing systems can offer the flexibility to create access points where users need them.
Where Else Can You Improve Structural Support?
Vibratory bowl feeder troubleshooting involves not just the feeder itself, but also how its support structure and connected machines contribute to performance and durability.
A lack of rigidity will sink you every time – the frame will vibrate instead of the material in the bowl. If you’ve used a T-slot frame, it’ll rattle to pieces under regular use.
Adjust or replace your industrial machine base so these key connections stay secure. To really bring it home, choose a structural framing solution that offers customization for different bowl sizes, shapes, and configurations.
For more guides on structural builds in industrial settings, visit our resource library:
Leave a Comment