Machine Structure Design: 5 Cost Reduction Techniques
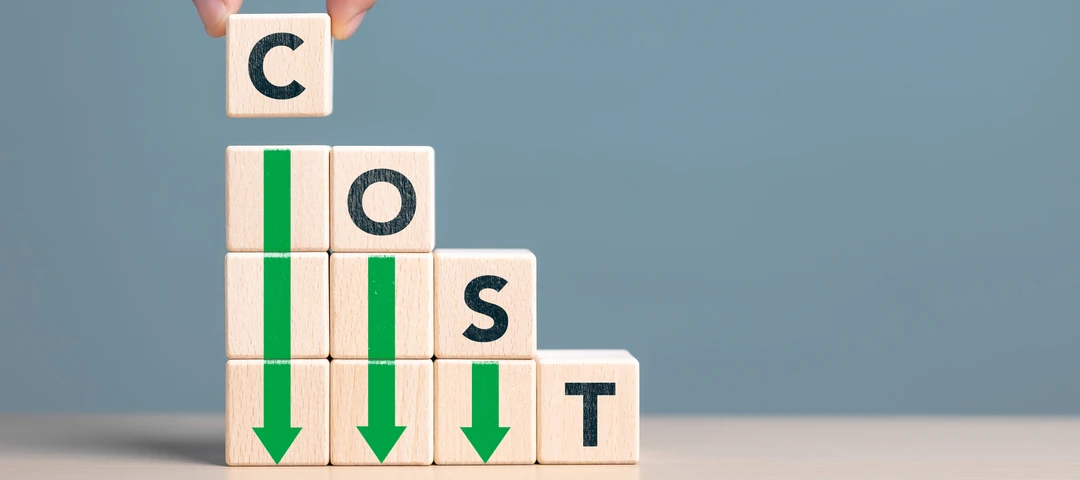
The most overlooked decision in industrial design today is how you’ll support the operation from not just from a process standpoint, but also structurally.
Equipment and machine structure design is often overengineered – or underengineered, depending on the framing system used. Hasty decisions based on “This is what we’ve always done” can lead to waste in material, assembly, and maintenance costs.
Let’s address your application with some actionable advice for reducing the up-front and long-term costs of modular industrial framing.
Top 5 Machine Structure Design Tips
Depending your production demands, these machine structural design tips could save you thousands in total cost of ownership:
- Don’t add downtime later to save a buck today
- Reduce assembly size
- Account for assembly & modification
- Stop welding when it's not critical to performance
- Use heavy-duty grade profiles … where necessary
1. Don’t add downtime later to save a buck today.
Choosing cheaper materials and building systems might seem like value engineering. But cutting corners in the wrong places can turn it into de-value engineering.
There are two main ways short-sighted design can rack up maintenance costs later:
Stability of Connections
Engineers put together industrial machine framing using either welded or fastened connections.
Welded framing creates fixed connections and continuity in the cross-sections. These permanent joints mean welded steel frames don’t loosen and come out of alignment due to:
- Vibration
- Cyclic loading
- Frequent movement
Fastener-based structural framing systems include aluminum extrusions and strut channels (i.e. Unistrut). These modular systems use some combination of bolts, nuts, screws, washers, and rivets to fasten profiles or plates together.
Popular bolted-connection systems include:
- T-slots – Extruded aluminum system of T-shaped profiles & brackets
- Strut channels – Sheet steel-based open channels with inward-curving lips for mounting
- Self-aligning – Extruded aluminum system whose angled fasteners & high-strength brackets replicate steel’s rigidity
These systems can look nearly identical at first – especially T-slot vs. self-aligning aluminum – but don’t mistake their performance as interchangeable. In rugged machine applications, results vary wildly:
Purchase Cost |
Maintenance Cost |
Performance |
|
T-Slot Extrusion |
Low-medium |
Very high |
Low |
Strut channel |
High |
Moderate |
Medium |
Self-aligning |
Medium |
None |
High |
You’ll learn more about the performance of these systems in #4 below.
Question to ask yourself: Are we throwing money at monthly maintenance due to failing connections?
Corrosion
Welded joints are more mechanically durable than bolted joints, but most welded framing systems are made of steel. So are strut channels. This puts both structural framing types at risk of rusting.
Vulnerability to corrosion adds maintenance costs in the form of routine recoating. In some harsh environments, there’s a bigger threat: Welded frames with openings (i.e. drilled holes) allow humidity and other moisture in. At first you won’t notice the flaking away of interior tubing, but you will when the frame crashes down and you have to replace it.
2. Reduce the assembly’s size.
It’s easy to get caught in the middle between light and sturdy.
The common way to reduce a frame’s material cost is to build with mild steel. It’s stronger and more rigid than competing aluminum materials …
… However, aluminum is a much lighter material …
… But there’s the pesky fact that T-slot connections are full of clearance and prone to loosening. Maybe it’s better to stick with steel after all?
If your design feels stuck in a gray area like this, try these solutions:
- Allow the experts to modify it. Instead of sending a bare-bones model with strict instructions, let the manufacturer review your idea and suggest a sleeker design.
- Integrate the assembly. Using a uniform framing type on a machine assembly (i.e. an enclosure’s base and guarding) can eliminate brackets and framework.
- Use self-aligning aluminum. The uniquely engineered connections automatically realign when vibrated, freeing you to use lightweight aluminum without extra supports.
Question to ask yourself: How constrained am I on size/shape requirement, and could another modular system do it in fewer parts?
3. Account for assembly and modification.
Think about the effort it’ll take to produce your structure today and each iteration after that.
Certified joint welders require a lot of manual skill (especially when joining aluminum), and their hourly rates are high. Mistakes lead to costly rework. You’ll also risk downtime if you don’t employ a welder in-house and have to wait for a third-party tradesperson to become available.
The accuracy of welds must be high for the frame to be level and square. The bigger and heavier the frame is, the harder that is to accomplish with steel. And the more you weld, the more potential there is for twisting and movement. You’ll almost always need to mill the profiles after the initial weld to achieve your desired specs. (Hope you have a CNC machine in-house!)
Is your design unusually large or reliant on a high number of connections? A weldless framing system will dramatically cut labor costs, both short- and long-term. Large steel assemblies made of weldments often require a team of people and heavy equipment.
Bring extruded aluminum into the picture, and suddenly labor looks a lot more palatable.
Extrusion and strut channel systems include slots along their profiles to allow for quick attachment of connectors and other accessories. Tightening bolts is a much simpler skill, and a lighter framework is easier to transport and configure with one person and a hex key.
From here, the options separate themselves a little more:
Good |
Better |
Best |
Strut channels |
T-slots |
Self-aligning aluminum |
Requires less skill than welding, but still made of heavy steel |
Lighter than strut channels, but often takes several attempts to align |
Lightweight and easy to slide on with precise alignment |
Unlike welding, aluminum extrusion and strut channel framing are absolutely doable in-house with your existing team. Bolted-connection systems are fabricated in a workshop, after which the manufacturer usually ships them for the buyer to assemble themselves on-site. Some T-slot manufacturers offer assembly services (at a price), while advanced, self-aligning systems come with subcomponents preassembled.
Depending on your structural demands, you may see additional labor savings by picking an advanced system. Often, you can assemble a self-aligning frame in 1-2 hrs., while an equivalent 80/20 aluminum or Unistrut structure will cost 4-5 hours of labor.
Modifications
Steel framing isn’t a user-friendly product – it usually has to be designed and engineered to perfection before you start, or else assembly will take even longer. If you want to make changes or fixes later, you’ll need to grab a welder again to cut off any unwanted parts and weld new ones in. In fact, you’ll have to relive all the time-consuming trouble of the initial build.
- Surface recleaning
- Post-weld machining to resquare parts warped by heating/cooling
- Repainting
- Shipping it around to various vendors
Even if you’re simply trying to relocate the frame to a new operation site, you’ll probably need multiple people and machinery.
Modular aluminum extrusions are easy to expand or even repurpose. The T-slot library includes hundreds of add-ons that are simple to slide or drop in after initial assembly. Self-aligning systems are newer and therefore have a smaller library, but what’s available is easy to add and realign without resquaring.
Question to ask yourself: How often will we move or modify this structure?
4. Stop welding when it's not critical to performance.
The graphic shows the range of demands that three popular machine framing systems can handle. There’s a canyon-sized jump between T-slots and steel weldments. This gap often leads to engineers either settling for T-slots that don’t meet minimum requirements … or weldments that are beyond their needs. In either situation, you pay more short-term (weldments) or long-term (T-slots) than is necessary.
Assuming your structural machine design will face some sort of adversity in its end-use environment, let’s focus on mid-to-high-range performance. A fixed connection is a must for any application with more light structural demands. In those cases, you can instantly eliminate T-slots and probably strut channels from contention.
But that doesn’t always mean you have to invest in welding.
Consider the chart above and where your application fits. If your project falls in the middle section, or anywhere reasonably close, a self-aligning system may offer the best total cost of ownership.
Question to ask yourself: Are the benefits of aluminum worth forgoing the extreme performance of welded steel?
5. Use Heavy-Duty Profiles … Where It’s Necessary
Has it surprised you that we’ve talked so much about connections while barely comparing the profiles themselves?
It’s a given that steel framing components will outscore aluminum ones in strength, fatigue resistance, and impact resistance. (This is true even though welding steel, and especially aluminum, decreases the profiles’ strength near the weld spot.) If your application is especially rough-and-tumble and could benefit from outstanding physical properties, steel’s the way to go.
But here’s another truth: Designers of steel and aluminum frames tend to overengineer them out of fear of structural failure. “Better safe than sorry” is an admirable outlook, but can hurt your bottom line.
One thing aluminum can do for you is leverage the superior strength-to-weight ratio of extrusion profiles.
This isn’t practical with traditional solutions. Because T-slot connections can’t resist moments, dynamic stresses sap the maximum power of those profiles.
Even when discussing profiles, strength almost always comes back to the connection. Most T-slot and self-aligning aluminum components are comparable in strength. The difference is in the connections (with an assist from rounded edges that distribute stress more evenly).
What’s this mean for the design? Self-aligning aluminum framing doesn’t create a weak spot at each connection. This gives you the flexibility to optimize the strength of each profile. You can use heavy-duty shapes where you need extra power, and standard-duty elsewhere – rather than paying for premium materials throughout the structure.
Question to ask yourself: Do my requirements for physical properties go beyond rigidity?
More on Total Cost of Ownership
A production line built with a weak structural system can lead to spotty product quality and damaged machines.
Choose the just-right modular framing system for your application’s demands, and you’ll avoid overspending on materials and maintenance. And by making assembly quicker and lighter – and with fewer parts – you’ll save on material and labor costs.
Want to know more about reducing your aluminum frame’s cost? Learn about other value improvements you can unlock by leaving T-slots behind:
Leave a Comment