Industrial Machinery Trends 2024
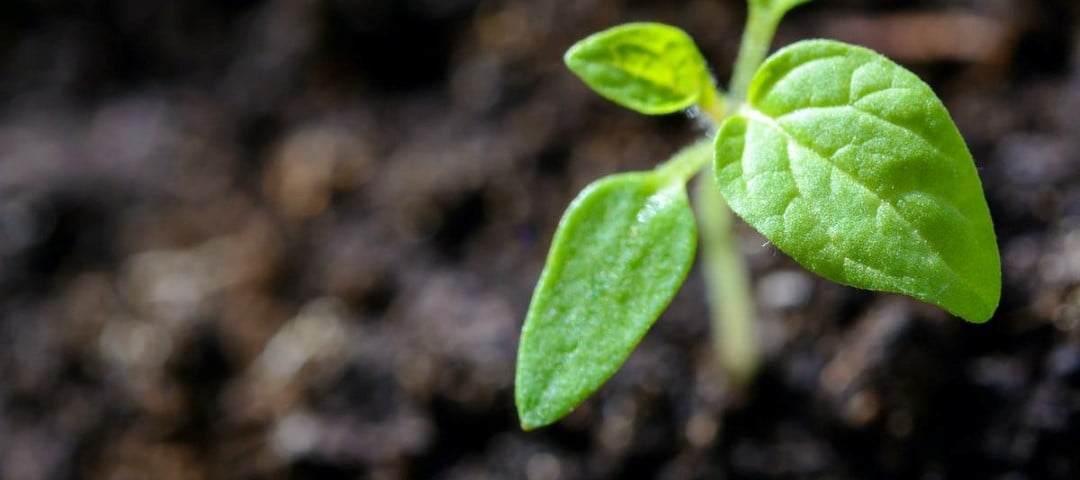
Manufacturers and product designers should always be looking forward. Luckily, there’s plenty to look forward to in 2024.
Look at the industrial leaders around us, and you’ll find tools and opportunities to grow in efficiency and quality. The new year is also a chance to re-examine practices that aren’t as effective or responsible as the old days.
These industrial machinery trends might affect your operation in 2024, both in general and specific to structural machine design:
- Lightweighting
- Ergonomics
- Structural automation
- UX
- Sustainability
- Customization
1. Lighter, Faster Design – What’s Driving This Need?
Lightweight design has been a dream of vehicle manufacturers for decades. The practice has recently spread beyond traditional and electric vehicles, into areas like automation.
The idea that lightweight and efficient designs can improve EV battery efficiency is, in a sense, translatable to industrial machinery and automation.
When an articulating arm or material-handling robot can move with less burden, it consumes less energy and can do its job more quickly.
How will engineers achieve sleeker designs without losing strength critical to performance? They’re already doing so by substituting steel for materials with better strength-to-weight ratios, like aluminum and titanium. As a bonus, lighter parts are easier to assemble and transport, saving labor and shipping costs.
Framing It for Structures
Improve strength |
Reduce supports |
Reduce weight |
Decrease cost |
If your perspective on aluminum is entirely based on soda cans, you’re not in 2024.
Aluminum framing systems are at the forefront of industrial design, offering lightweight alternatives to traditional welded steel. Aluminum profiles may have lower tensile strength, but they’re also nearly 3x lighter than standard steel profiles. In the end, aluminum extrusions give you about 2x the strength-weight ratio vs. steel weldments, making them a viable replacement in lightweighting applications.
Traditional aluminum building systems have a knack for rattling loose in dynamic applications, limiting their usefulness. That’s what makes a newer alternative to T-slot extrusions – self-aligning aluminum framing – such an exciting trend. This system still consists of aluminum extrusions, but creates weld-like rigid connections via angled fasteners and high-strength brackets. The result is a mechanically locking assembly that requires fewer cross-bracing components, and less material overall.
Welcome to 2024.
2. Ergonomics in Industrial Spaces
Assembly, packing, testing, transport … There are many areas where bad ergonomics can harm productivity, yet some companies think the concept only means “comfy chairs.”
What about the hardworking folks on the plant floor? Chances are their day-to-day involves at least one – if not all – of these safety threats:
- Awkward postures
- Lifting
- Using excessive force
- Repetitive motions
Ergonomics should have a seat at the table (hopefully an ergonomic one) when designing industrial spaces. That includes the equipment and machinery employees will use in that space. Comfortable, flexible work areas reduce time off from long-term injuries, improve productivity, and boost employee morale.
Industrial ergonomic products include:
- Desks & tables – extendable length and height so they’re comfortable for everyone
- Benches – user-friendly while still suitable for heavy-duty settings
- Equipment workstations – easy to tear down and reconfigure as needed
Framing It for Structures
Modular framing systems make work spaces even more user-friendly, both on the manufacturing floor and in the offices:
- Slide components on and off as you please
- Extend tables, desks, & benches for more room
- Reconfigure stations to different heights
Modular framing’s on-the-fly adjustability allows it to cater to different work shifts and project focuses.
The need for modularity disqualifies welded assemblies from being good fits for ergonomic industrial products. Bringing in a welder to modify or repair equipment is neither time- nor cost-efficient.
From there, it’s more in how you design with the product than it is the product itself. Any non-permanent metal connection system can help your ergonomic initiatives, provided it’s stable enough to handle nearby vibration and possible impacts.
Of course, if you can’t beat ’em, join ’em. You can lessen the need for ergonomics by putting more effort into #3 …
3. Automation, the Structural Way
For the industrial process, automation is becoming less of a bonus and more of a “make-or-break.”
Unsurprisingly, Grand View Research says the worldwide market for industrial robotics will grow at a 10.5% compound annual growth rate between 2023 and 2030.
Mobile robots (or cobots) can eliminate the need for humans to do repetitive tasks. This frees workers up to tackle jobs that are more brainpower-dependent and less menial.
Done correctly, there are many other benefits of production and material-handling lines adopting more automation:
- Increases production rate
- Reduces human error
- Sidesteps labor shortages
Framing It for Structures
In automation environments, components simply can’t be out of place, so structural components play a huge role in success.
Engineers are integrating metal framing systems into automated assembly lines, workstations, and storage and retrieval systems. For them to continue as a pillar of the automation revolution, these structures must – and will – become more efficient and structurally reliable.
Currently there’s a lot of under- and overengineering going on in automated-machine building. Some designers under-engineer machine bases and sensor mountings by specifying T-slots, which causes safety or quality issues when the connections inevitably slip out of alignment. Other designers overengineer by specifying steel for automation builds that don’t require such a high level of sturdiness. In mobile situations, this results in a machine that either moves slower or burns more energy.
One solution is to find the middle ground with self-aligning aluminum framing. Since this system combines the lightness of aluminum with the rigidity of steel, it can add efficiency and durability to your existing solution. You can even consolidate hybrid machine assemblies into a single self-aligning frame.
4. User Experience (UX)
Restaurants, shipping packages, and other products and services have gone all-out to sell and separate themselves as an “experience.” While industrial machinery or equipment doesn’t need to make its user warm and fuzzy inside, it does need to meet today’s expectations for UX.
In 2024, there's already an amplified focus on ease of setup and interaction in structural designs. UX-first design:
- Reduces risk during maintenance & installation
- Boosts speed of operation
- Reduces physical strain on workers
Framing It for Structures
There are a few broad ways structural framing can greatly improve UX this year:
- A combination of trend #s 1-3. Using high-strength components where you need them – and only there – ensures your assembly is secure without being too bulky. This optimizes the amount of bracketry and cross-bracing necessary, reducing the time and heavy lifting you’ll have to invest in assembly and upkeep. It also reduces obstruction for the operators and maintenance crew, meaning there’s less risk and hassle involved.
- Use of rigid assemblies. Having to tighten, check squareness, loosen, and retighten connections several times over isn’t exactly the definition of user-friendly. Expect to see more durable connection systems in vibratory and high-movement settings going forward. Replacing crudely engineered T-slots with self-aligning aluminum or welded steel systems can get you there. Self-aligning aluminum slides on with instant precision to cut assembly time by 50%, and its mechanically locking nature means there’s zero maintenance – ever.
5. Sustainability
“Industry” is responsible for 23% of greenhouse gas emissions, according to a 2023 report by the Environmental Protection Agency. Despite this, machinery and manufacturing are lagging behind other sectors in committing to carbon-output reduction.
With so many of its processes resource-intensive, industrial production has a responsibility to be more, well, responsible.
There’s more to sustainability than just curbing carbon, with emphasis growing in recent years on agency regulations for eco-friendly materials and other practices. That’s not to mention customers’ own expectations.
Efficient industrial equipment and processes use less energy and waste less material. Choosing the materials themselves, and the manufacturing method, more wisely can also help.
In recent comments about digital tools, Siemens made an interesting point about design impacting sustainability:
“... Perform evaluation and analysis in the realization phase when planning a product’s design and the machinery that will manufacture it. This is the perfect time when you can decide about energy-efficient equipment and how long that product will last. We hear people talk of brownfield factories, but there are also brownfield designs (existing designs that you are trying to make more environmentally friendly), which are more complex than starting fresh with the information you need to make them environmentally friendly from the beginning.”
Maybe it’s time to rethink our materials and processes from scratch.
Framing It for Structures
Aluminum framing is easier to recycle than steel because of its low melting temperature – you can practically melt it at home. Because aluminum naturally forms a self-protective oxide layer when exposed to the elements, it’s also usable for much longer than steel in corrosive environments.
And, of course, the modularity of aluminum building systems will continue to make it a popular choice for repurposable designs. You can take apart extrusion and tube-and-joint structures if they’re no longer relevant to your operation, and use the parts for something else.
Does Your Design Take Advantage of Industrial Machinery Trends?
Looking forward to the rest of the 2020s yet? Machinery, automation, and industrial equipment still have much room to grow.
Lighter and smarter design can improve material usage, user access, and assembly speed. More thoughtful design can seamlessly merge the user-friendliness and environmental responsibility.
All of this is possible without compromising on structural integrity.
To get more insights on modular industrial design, visit our blog library:
Leave a Comment