Industrial & Machine Door Design 101
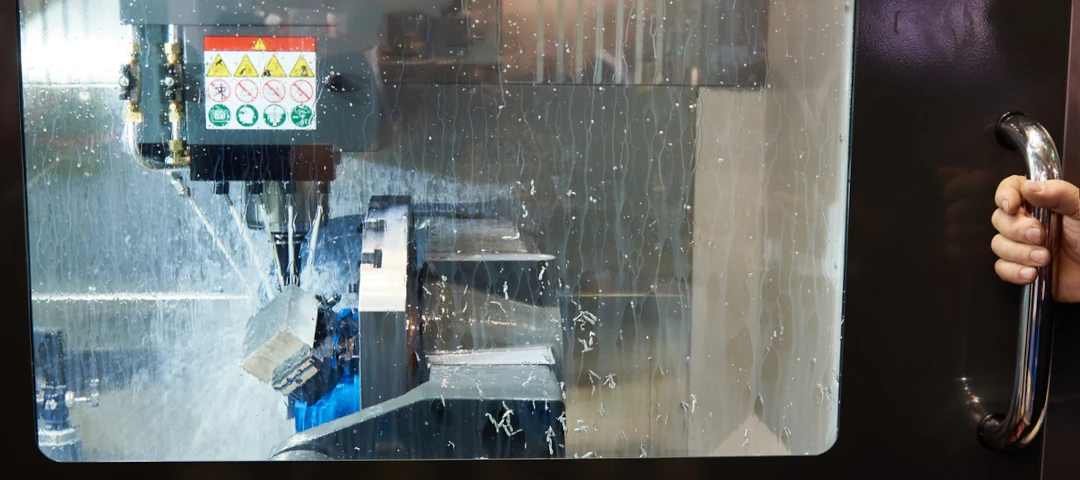
Until one suddenly fails, operators often take doors for granted.
For the sliding-screen entry to your backyard, failure isn’t a big deal. In an industrial application – say, an automated machine safety door – failure is a physical and financial hazard.
Don’t learn this lesson the hard way. The right industrial door design can reduce maintenance and repairs, save space, and uphold safety standards.
These study tips will open new building possibilities you didn’t know existed for machine doors and other heavy-duty equipment:
7 Tips for Industrial Door Design
Your industrial door frame can benefit from seven surprisingly simple design conversations with your engineering team:
- Types of doors
- Hinges
- Thresholds
- Materials
- Finishes
- Self-assembly
- Replacing the door vs. replacing the whole structure
1. Know Your Industrial Door Types
There are four main types of industrial doors. Your choice will largely depend on space availability and performance needs.
Standard
Standard doors for machine and other heavy-duty uses are much like your everyday hinged door, but on industrial-grade steroids. It’s common to pair them as double doors (often called French doors).
- The bad: Standard doors may lack accessibility and visibility in some industrial uses.
- The good: High-performance hinges make a big difference, meaning there’s opportunity to build a rigid framework that’s more than “standard”
With the right system, a hinged industrial door can support up to 1,500 lbs. (More on this in section #2.)
Bifold
Bifolding industrial doors open by folding back in sections, or “panels.” Despite the name, they often have three or more sections to form an “accordion-style” door.
- The bad: Standard T-slotted framing needs frequent retightening due to precision errors and generally coming loose from everyday use.
- The good: When done correctly, it’s the most resilient and universal industrial door system design available.
Because many automated bifolding industrial door systems leave potential on the table, we’ll throw in a few other goals you can meet with this style:
- Maintenance-free – If you update from T-slots (see section #4)
- Space-saving – Conserves square footage in a factory
- Access – In certain applications, helps operator safely access structure
Lifting
Lifting industrial doors are hingeless, relying on a spring assist or counterweight for support (like a manual garage door). During movement, the door rolls along a track profile. The counterweight “stay” feature keeps a door, lid, or cover from crashing down after the user lets go.
- The bad: Loose or otherwise degraded connections can result in the door slamming, injuring the user.
- The good: It’s a great option in spaces where there’s more head room than in front of the structure.
Horizontal Sliding
Horizontal sliding/folding doors (also called pocket or sliding barn doors) use most of the same components as lifting systems. An industrial sliding door track system is hingeless and relies on proper alignment to operate smoothly.
Unlike liftoff systems, sliding doors usually don’t need a spring assist or counterweight because gravity isn’t a factor in most applications. Systems for very heavy doors can be an exception and include a counterweight.
- The bad: Some have too much friction or cheap bearings, resulting in misalignment or excessive resistance when opening and closing
- The good: Ideal for areas with minimal head room or wide openings (up to ~14 m)
Industrial and machine sliding door designs are meant for high-use applications on a budget. They’re less insulation-friendly than swinging doors, and this reduced sealing makes them a little less safe and a little quicker to age. Remember that choosing lower-performance materials and engineering methods can create extra hurdles later.
2. Verify What Your Hinges Can Hold
The goal is smooth, safe operation, and much of that falls on the profile system’s connections.
In liftoff industrial door solutions, welded steel and other heavy materials aren’t ideal. Naturally, the heavier the door is, the more you’ll have to invest in counterbalancing and heavy-duty components. For sliding and other door types, steel is much more compatible, though it’s challenging to align the heavy materials.
Verify what your machine door hinges are capable of before committing to a final design. Whereas steel machine doors can get expensive, T-slot aluminum door framing doesn’t cost a lot up-front – for good reason.
Typical T-slot hinges are spartan in design and therefore not super precise. As such, they easily come out of alignment, causing the door to sag, along with other maintenance problems. It’s a crapshoot whether the pins will align again or you’ll have to loosen and realign everything.
Why not find some middle ground between steel and T-slots?
Today, advanced aluminum extrusion framing exists for that very reason. This option uses angled fasteners and high-strength bracketing to optimize profile performance and maintain precision. With self-aligning technology, your frame can support 1,500 lbs. with a hinge at 90° and 1 ft. out – without losing its alignment.
For doors, that means:
- No sagging due to constant vibration
- No sensor faults
- One less source of downtime
3. Don’t Neglect the Threshold
An industrial door’s threshold completes the door-frame assembly, helping form a fully enclosed box. Including a proper threshold is surprisingly important to the application-specific function of many industrial metal doors.
When choosing types of thresholds, consider what’ll be on both sides of the divide. Depending on the structure involved, the threshold may need to keep out:
- Dust
- Fire
- Contaminated air
- Temperature differences
- Moisture
- Noise
Another trait typically reserved for heavy-duty thresholds is the ability to withstand extreme stress loads. This is valuable in the case of doors through which heavy equipment will pass frequently.
Some of these characteristics are shared by most thresholds, while others require a more nuanced solution. For example, most thresholds are fire-rated to meet UL 10B and 10C safety standards. However, areas with major temperature disparities are best off with a thermal break door threshold. For noise cancellation, you’re better off with a specialized acoustic threshold.
4. Materials Matter
Know your project! Your material choice will depend on your needs for:
-
Function of attached assembly
-
Cycle life
-
Budget
Industrial Door Material Comparison
Up-Front Affordability |
Stability |
Lightness |
Strength |
Corrosion Resistance |
Ease of Use |
|
Carbon Steel |
Medium |
High |
Low |
High |
Very |
Low |
Stainless Steel |
Very |
High |
Very |
Medium |
Very |
Low |
Alum., |
High |
Very |
Medium* |
Low |
Medium |
Medium |
Alum., |
Medium |
Very |
Medium* |
Medium |
Medium |
Very |
(*T-slot parts are lightweight, but they’re also weak. Self-aligning systems are made from similar aluminum materials, but require far fewer parts to achieve the same strength.)
Historically, steel–framed machine doors have outperformed their aluminum extrusion counterparts. Engineers sometimes go with steel by default because they think that’s what they’re “supposed to do” for industrial or heavy-duty builds.
This logic is half-correct. While some aluminum building systems do struggle with stability, an extrusion can hold more weight than you think.
Aluminum T-slot framing designs that rely on hinges will always create compounding precision errors – and the need for frequent retightening. They’re also inherently weak at their connections, failing to leverage the full strength of each profile.
However, with auto-aligning aluminum systems, it’s basically impossible to mess up the precision. And while a standard aluminum profile is 35-40% weaker than a steel profile of the same weight, steel is nearly 3x heavier. Pound-for-pound, aluminum is more than 2x stronger than steel.
All that to say … self-aligning aluminum framing can be a viable option for combining the lightness of T-slots with the sturdiness of steel. Just make sure aluminum meets your other property needs.
Some other facts that may affect your application:
- Heat: Steel is more of a burn risk because it holds heat longer, but it also has much more structural tolerance for high temperatures. Aluminum dissipates heat much more quickly, but isn’t ideal for structural applications above 200 °F.
- Sound: Aluminum is a great acoustic absorber.
5. Finish Strong
In the industrial world, even indoor applications need protection. The end-use environment may have potential contaminant, corrosive, or collision at every turn.
Industrial finishes’ first priority is protecting the assembly, with aesthetics usually a distant second. Certain surfaces don’t work well in high-precision applications, so keep that in mind as you budget.
- Paint – This is the most common, least expensive, and lowest-quality coating option. Painted carbon steel is still more prone to rusting than galvanized steel, stainless steel, and aluminum. It also offers only 10% of the abrasion resistance that galvanization offers. Painting best works with standard steel (i.e. if you want a “safety yellow” color).
- Powder coating – More expensive than painting, this option provides a thicker, more even coat. Powder coating can change dimensional thickness, which is a slight problem for T-slot doors and a nonstarter for self-aligning aluminum systems. Messing with the tolerances of high-precision framing kind of defeats its purpose.
- Anodizing – Exclusive to aluminum, this finish improves corrosion resistance. Treatments are available in black, clear, and bronze. Self-aligning systems use an architectural-grade version that further ensures flaking particles don’t enter your sensitive operation.
- Galvanizing – This mid-range option adds a zinc layer to bare steel to improve its corrosion and scratch resistance. You can even combine it with a paint layer to double up on protection. On the downside, its roughly textured surface is a pain to clean.
There’s one final option: the “au naturel” (yet very expensive) look. Stainless steel doesn’t need a secondary finish because it’s already corrosion-proof, impact-resistant, and appealing. Its surface is sterile and easy to clean, making it ideal for medical and cleanroom applications.
6. Put Assembly in Your Own Hands
Door frame assembly is easier than it used to be, whether you’re talking about 5 years ago or 100.
We’ve all been in an early 1900s house and noticed how it’s shifted over time. The doors stick because the frame’s crooked, and may never have been built straight in the first place.
Many modular structural system manufacturers offer to assemble the kit themselves for an extra fee. Unless you’re truly strapped for time and help, save the money and assemble it in-house.
If you value a modular experience (both in initial build and later modifications), consider choosing extrusions over welding. In addition to being the fastest and easiest installation, extrusions also eliminate the cost of paying a skilled welder.
Today’s aluminum doors are usually easy to assemble – just a rectangular frame with a couple of brackets on it. Using a modular aluminum building system makes it even easier to integrate the door with the rest of the structure.
If you want to invest in the easiest solution and reduce assembly time and labor by 50%, go with self-aligning aluminum.
Why self-aligning aluminum? The mechanically locking joints slide on with instant precision. They’re simple to install, undo, and reinstall with just one person and a hex key.
Especially with hinged doors, the system is a godsend – you just put them on one side, tighten the door, and you’re set. Having a squared-up door frame is critical to a successful installation. Doing manual lineup with traditional T-slots is possible, but requires extra care.
7. Replace the Door & Frame Assembly, Not the Entire Structure
At home, would you replace all four bedroom walls because you hated the framework on the entry door?
You don’t have to replace a whole structure to get a better door.
For a more relevant example, think of a typical CNC machine door design. As a whole, the CNC structure includes:
- A welded steel machine base
- An enclosure door
- T-slot guarding
If the door’s sagging, build a sturdier (self-aligning) aluminum frame around the opening, using universal brackets to mount it to the existing structure. Industrial door replacement is achievable with $1,000 – much easier to swallow than $25,000-$35,000 for the machine guarding, base, and door.
More Checks & Balances for Your Heavy-Duty Door
Damage and weak points are minor nuisances at first, but they can grow into long-term safety and efficiency issues that disrupt your production routine.
With the right design and engineering mindset, you can create industrial door systems that last for decades – no matter how much operators (mis)use them. Your structural framing system manufacturer can help you balance project-specific needs in:
- Strength
- Precision
- Durability
- Modularity
- Cost
Interested in the AngleLock method of door improvement?
Leave a Comment