AngleLock Develops Modular Aluminum System as Rigid as Welded Steel
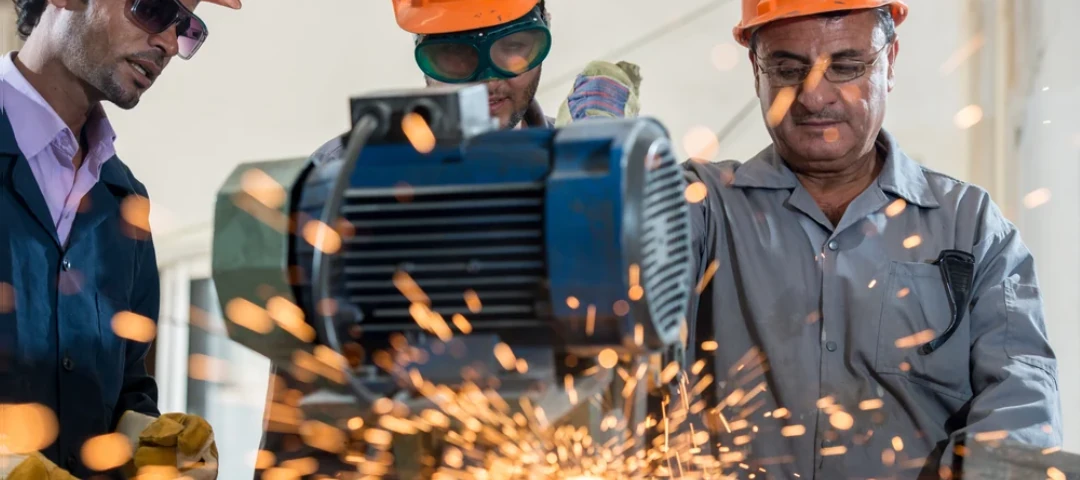
For a half-century, designers have looked at aluminum framing as a cheap, quick-fix alternative to stronger materials and engineering methods.
Until recently, there’s been no evolution of the product that could meet the reliability needs of manufacturing, automation, and other industries. AngleLock, a spinoff company of Controlled Dynamics, has solved that by bringing a more durable aluminum system to the structural framing market.
“AngleLock is without question the strongest, most stable, and most versatile framing system in the business,” says customer Greg Gernert, VP and general manager for motion Control Business at Rockwell Automation.
How could aluminum framing, perceived as softer and weaker than steel, create connections that last?
How Does AngleLock Create a 100% Predictable Connection?
When building machinery, equipment, and other industrial-grade structures, engineers often choose between welded steel and T-slot aluminum. This is a one-or-the-other approach that leaves potential on the table:
- Steel offers strength, alignment, & unobtrusive design
- T-slots offer lightweight modularity, low initial cost, & corrosion resistance
- AngleLock offers all six
Because their connections fail under dynamic conditions, traditional aluminum frames are inefficient in industrial settings (unless they’re welded, but that method creates several other issues). But AngleLock is anything but traditional.
AngleLock’s patented technology creates fixed, weld-like connections that maintain alignment within microns, even in dynamic environments. Adapted from another successful Controlled Dynamics business, the concept uses high-strength brackets with predrilled holes, along with angled bolts and screws. The fasteners remove clearance and square the framing perfectly, and when vibrated the bolts stretch like a spring and snap the connection back into place.
In other words, unintentional loosening of an AngleLock connection is physically impossible.
Value Gains Over Welded Steel
It’s obvious to see how a mechanically locking system would outperform other aluminum framing, but AngleLock also solves the problems steel frames create.
Welded frames help users avoid maintenance and downtime costs from sagging enclosure doors, misaligned sensors, and other failures in strength and rigidity. However, the added costs in materials, skilled labor, lead time, recoating, and modification negate their initial value.
AngleLock connections optimize the strength of each profile, allowing users to use lightweight aluminum without fear of structural failure. Subcomponents come pre-assembled; putting the rest together requires one modestly skilled person in-house and one hex key. Since the components slide on and off, modifying an existing AngleLock build is easy to do with instant precision. Adding to the value, the parts undergo architecture-grade anodization so there’s no need to recoat them in most environments.
Where Are Engineers Replacing Steel With AngleLock?
As this video demonstrates, AngleLock is a definitive answer to total cost of ownership in framing for many applications inside and outside the factory:
- Integrated bases & guarding for machine enclosures
- Benches, workstations, carts, & racks
- Entertainment & events – staging platforms, display cases, & aquarium tanks
There are countless creative uses for structural framing, and in most cases AngleLock offers better utility and cost efficiency than welding.
“AngleLock gives us a competitive advantage, and we will use it for all integrations moving forward," Gernert says.
Learn More About Rigid Aluminum Framing
AngleLock creates a vast middle ground of design possibilities, helping companies avoid unnecessary expenses from welding and maintenance downtime from traditional T-slot systems.
There are two ways learn more about rigid, modular framing:
- Head to the AngleLock main blog page and browse the free resources.
- Visit WESTEC (Nov. 7-9, 2023, in Long Beach, Calif.) and talk to an engineer at Booth #2003. (Trade show booths are, ironically, another great application for AngleLock.)

Leave a Comment