Maintenance Downtime Reduction for Steel & Aluminum Framing Systems
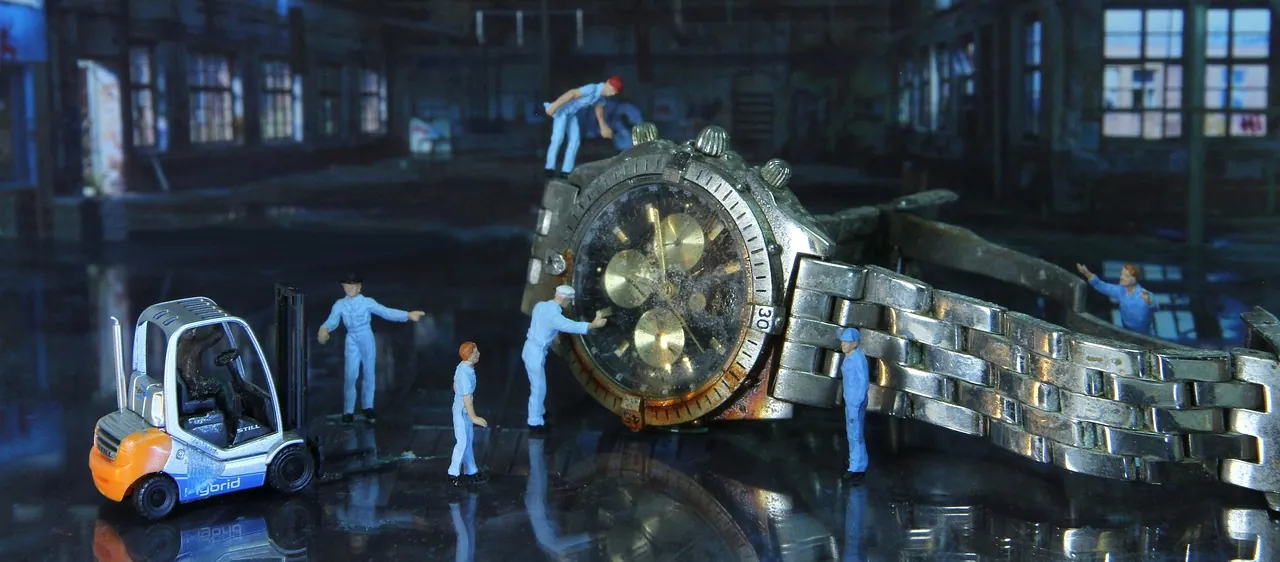
If T-slot aluminum framing is abundant in your factory, it’s a virtual must that you staff a maintenance guy to regularly check its alignment. And if you rely heavily on weldments, you know steel frame maintenance is a pain thanks to all the flaking paint and limited ability for adjustment.
These are just two of the many hassles of maintaining steel and aluminum structures. But are they truly necessary evils, or avoidable compromises?
Let’s uncloud what’s real and what’s waste so you can reduce maintenance downtime – both planned and unplanned – in your industrial framing application.
Structural Frames & Reduced Maintenance Downtime: 5 Factors at the Factory
Depending on your material and manufacturing choices, maintenance downtime reduction for structural framing systems boils down to:
- Sagging connections
- Inaccurate results
- Surface upkeep
- Safety fixes
- Replacing lost causes
1. Sagging Connections
Projects involving industrial doors are something of a design (and financial) mirage.
In many modular structures, the biggest source of downtime is a droopy door or sagging stand. This happens when engineers use T-slots, whose connective components are clear weak points in the assembly. On doors with T-slot framing, you’re also stuck using unreliable hinges that are tough to realign.
The obvious alternative is a welded steel frame, which offers much higher strength and long-term durability. This comes with the other general benefits of steel, but also causes you to give up the perks of aluminum (i.e. light weight). It also means you have to replace a large portion of the structure, an unwelcome cost.
What if you could keep aluminum as your material – and save part of the structure? While you can’t save your original entryway, you can keep thousands of dollars.
Because T-slots dominate the market despite being a crudely engineered technology, there are misconceptions about how much weight an aluminum extrusion can hold. Today, there are modern alternatives to T-slots that use self-aligning brackets, inserts, and other connections to optimize the strength of each profile. This grants a structural frame the strength of steel, but with the lightness of aluminum.
By installing a sturdier aluminum frame around the opening, you can replace the existing door, but keep the rest of the enclosure. (This strategy works with windows too.) Simply build a self-aligning frame around the door, then insert the new door.
Machine enclosures can cost $25,000-$35,000 – replacing only the door saves all but ~$1,000 of that investment.
2. Inaccurate Results
Many industrial applications rely on ultra-precise technology to produce quality at a rapid pace. This is particularly true in automation and other use cases with heavy vibration.
When the fixer-uppers have to jump in because a machine’s not working properly, the finger of blame sometimes points in the wrong direction.
“We keep replacing sensors because it’s giving bad readings,” is a common complaint about automation machinery. Often, in reality the sensor is fine – it’s just misaligned.
If a machine won’t start because a misaligned sensor claims the enclosure is open, that’s a waste of time in both upkeep and production. If a quality-control sensor’s alignment comes loose, you could produce an entire batch of bad widgets, which costs time while the team investigates, not to mention redoing the order.
This is why you should think of aluminum and steel framing design as two different things, and even more so, T-slot aluminum vs. self-aligning aluminum systems.
Say you’re assessing the costs of preventative maintenance for a CNC machine or a vibratory bowl. Steel framing is stiff and doesn’t slip out of alignment when something bumps it or causes vibration. Some folks don’t know how to use T-slot aluminum (or are misled by vendors about its sturdiness), so they drop it into applications for which it’s wildly ineffective. It quickly loosens and weakens over time, making it a constant maintenance hotspot.
However, self-aligning aluminum frames tighten with vibration because they’re engineered with angled bolts and high-strength bracketing. Much like structural steel, they eliminate the need for routine tightening.
3. Surface Upkeep
This facet of maintenance is more widely understood, but is still worth a reminder.
Steel corrodes easily in applications subject to moisture or harsh chemicals. You can regularly recoat the surface, but that’s not only time-consuming, it’s also only modestly effective.
One of the biggest advantages of aluminum framing systems vs. steel is the former’s ability to protect itself innately. Thanks to the presence of zinc, aluminum alloys form a natural oxide layer that slows corrosion. You can double down on maintenance downtime reduction by adding an architectural-grade anodized coat to your aluminum.
After that, surface upkeep of an aluminum structural frame is simply a matter of wiping it down when it gets dusty.
There’s one small asterisk – let’s return to the enclosure door example. If you remove a T-slotted door for cleaning, you’ll struggle to realign the lift-off hinges. Because of this, maintenance workers tend to clean the door in place.
With self-aligning framing technology, you can easily take off the door for cleaning and reaffix it with instant precision.
4. Safety
The more safety issues your design choices make, the more the maintenance crew will have to save the day.
- Poor operator visibility & access from weak, overdesigned T-slot systems
- Failing frames endangering nearby people & machines
- Heavy, cumbersome components that are a chore to move
Asking operators or the maintenance team to constantly go in and fix the framing is not only wasteful, it’s also an injury risk in itself. One example is locking out equipment and ensuring nobody turns it back on while the worker is fixing it. You can probably think of other scenarios.
Safety mishaps are a long-term cost you can easily avoid by avoiding cheap, short-term designs.
5. Replacing Lost Causes
The above issues all tend to lead to premature death for a modular framing system.
Steel framing systems usually last for years as a stable option you can mostly set and forget. Sadly, they corrode over time and become bulky as you add support fixes – consider aluminum in harsh environments or when you expect frequent modifications. When a steel frame becomes too ugly or corroded to use, the maintenance crew will have to prep a replacement system all over again.
Meanwhile, self-aligning framing should replace T-slot extrusions in dynamic and high-performance applications that require aluminum. The life span of an extruded T-slot frame is just not worth it in terms of maintenance and other downtime costs.
If your modular framing does use T-slots, there are preventative measures that can extend its useful life:
- Industrial-grade adhesive (i.e. Loctite) – Like super glue for nuts and bolts, it keeps parts from coming loose. However, some grades require heating to loosen it back up. Also, while the screws won’t come loose, the brackets can still be knocked out of alignment because the connection relies on friction.
- Dowel and spring pins – By drilling holes and installing pins, your connections can get a step closer to permanent. But if you later have to move a pinned bracket even a little, you’ll have to drill a new hole.
- Welding – Bonding aluminum T-slots like you would a steel frame helps them stay tighter longer. Unfortunately, welding aluminum is more difficult and may require you to bring in a third party with this uncommon skill. Plus, this process reduces material strength around the weld location.
These workarounds can be much more time-consuming, a little more expensive, and a lot less modular than going the easy route (self-aligning framing).
Why Schedule Maintenance Downtime in the First Place?
Where are users experiencing the most preventable downtime?
Having to do it in the first place.
Depending your application, you’ll find a very different maintenance experience behind:
- Door #1: Easy-to-use T-slots
- Door #2: Powerful steel
- Door #3: All of the above
Self-aligning systems are that “best of both worlds” option, though not every project is a match. The devil is in the details of your performance requirements and budget.
To learn more about structural builds for industrial applications, visit our blog resource center:
Leave a Comment