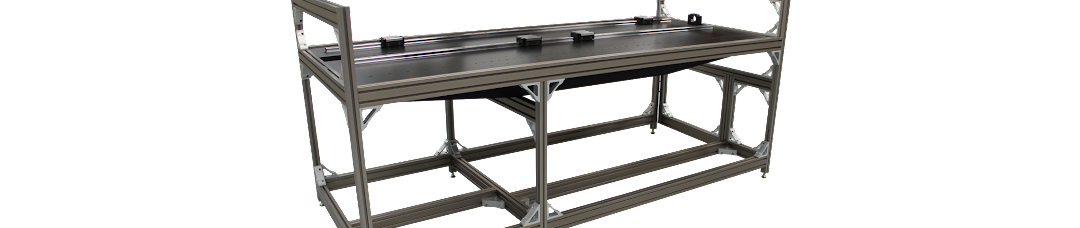
7. Be Smooth. Be Round. Be Aesthetic
With self-aligning aluminum framing, there are many ways to get creative for both form and function.
For example, specifiers question the 70/70 corners on AngleLock components – they're not used to seeing a profile rounded with a slot at a 45-degree angle. The components are this way for a reason.
Almost everyone would agree that sharp profile edges create an unattractive “industrial” look.
AngleLock profiles and brackets come with rounded edges, creating cleaner-looking assemblies. And because the system can use three-way corner brackets, you can use fewer eyesore brackets and have more open slots for panels.
You’ll immediately notice a sleeker, more attractive feel to a rounded system. The smoother appearance reflects light better and gives a modern, seamless, and approachable vibe.
Of course, this is just one example of how AngleLock makes aluminum framing viable in public-facing projects. Consider how you can integrate these other opportunities for user experience:
- Eliminating the need for cross-bracing means better sight lines and reduced obstruction.
- Architectural-grade anodizing on profiles is available (only with AngleLock) in black, clear, & bronze to protect your frame’s look and integrity from outside elements.
- Because the system stays together without maintenance, there’s no need to tack on bulky additional supports as the frame weakens.
Involving the Supplier in Your Aluminum Structure Design
Pairing aluminum extrusion profiles with stiff connectors gives you nearly unlimited freedom to make your design the star of the operation.
Engineers and designers want to do things their way, and that’s OK – there’s nothing wrong with back-and-forths with the manufacturer. Just make sure you’re having these (often eye-opening) conversations, whether it’s for a new or revised concept.
Because AngleLock assemblies thrive in dynamic applications, there may be opportunities to expand your use of aluminum. For example, a machine enclosure assembly once made from a T-slot and steel mishmash could become a single AngleLock assembly.
To innovate in ways you didn’t think were possible, start by checking out our Design Assistance page:
Leave a Comment