Building With Aluminum Extrusion: Designing Modular, Adjustable Frames
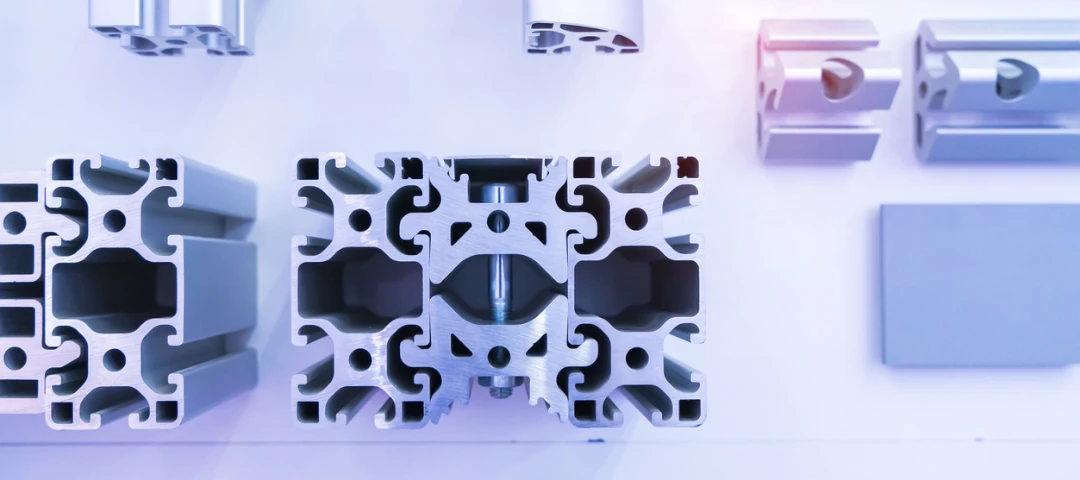
Aluminum extrusion is a valuable material process for creating structural frames – when engineers use it correctly.
Engineers are smart folks. But not all the building blocks they have to work with are created equal. And not all engineers understand how to maximize the potential of aluminum framing systems.
Using design techniques that prioritize modularity and adjustability makes projects easier on your crew. You’ll save time fussing with assembly and disassembly, and avoid the costs of hiring outside help.
When building with aluminum extrusion for a structural framing system, use these tips for easier first-time assembly and future modifications.
Building With Aluminum Extrusion Frames – For Easy Assembly
There are several ways you can make initial assembly faster and easier with smart engineering and the right framing components:
- Fastener orientation
- Mistake-friendly materials
- Lightweight design
- Assembly size
Orientation of Brackets & Nuts
Nuts are about as standard as it gets for fastening options on T-slot profiles. With traditional T-slots you don’t have to worry about nut orientation, but you do sacrifice joint strength.
When using self-aligning aluminum systems, sometimes the engineer slips up and fails to consider the orientation of nuts, bolts, and brackets.
Sometimes this means having to turn a nut a certain way so it fits. How many stories have you heard (or experienced yourself) of having to take off a plate or panel multiple times to address this? While self-aligning systems require you to be more mindful of orientation, you gain the benefits of stronger connections and easier access.
Keep Your Design Revision-Friendly With Aluminum
Stay away from welded steel if you have a design that’s complex or you’re unsure about evolving, long-term needs.
Say you start building, but unknowingly work off the wrong document version. … Did you use welded steel or aluminum extrusion framing? One “oops” will cost much more time and money than the other.
Another example: Say there’s a late change to your industrial machine design. You freak out, dreading the 2-week delay while you return it to the manufacturer or the cost of having a technician fix it on-site. However, with the right modular system, your design might not need to leave the facility or require special skills to modify.
Aluminum framing is easy to move and doesn’t require a skilled welder to assemble. Options on the higher end of the quality spectrum realign with instant precision, with only one worker and a hex key necessary.
Lightweight
Remember that the way you build with aluminum framing doesn’t have to mirror the steel frame designs of your past.
Come assembly time, a large steel weldment might require a forklift for moving around and jib cranes or gantries to install sections of the assembly. And if you don’t have heavy equipment readily available, that’s an extra time and money sink.
If you stick to aluminum wherever possible on the design, arranging the pieces might only require 1-2 people and no forklift.
The cross-sectional area has a huge impact on the assembly’s total weight. The more rigid your system is, the fewer brace supports you’ll need. Sound like a paradox?
- Steel is stiff, but heavy
- T-slots are ~3x lighter, but have weak connections
- Self-aligning aluminum extrusions, a high-end T-slot alternative, are engineered to mimic steel’s stiffness while staying lightweight
If assembly of cumbersome items is putting stress on your team and your wallet, consider investing in self-aligning structural framing. These systems use angled bolts and high-strength connections to maintain precise alignment. They’re the perfect in-between if you want convenience for both today and tomorrow.
Decrease Assembly Size
No Ph.D is necessary to understand shrinking your build can make the job ...
- Easier
- Faster
- Cheaper
This is another design strategy where the decision to build with T-slots vs. high-end alternatives will impact results.
By using sturdier corner connections, you can reduce the number of crossmembers and brackets in your assembly. You can rule out T-slots in this situation – much like welded aluminum joints, their connections are their weak points. By creating mechanical locks rather than relying on a pinned connection (pivots and friction), self-aligning framing connections are stronger and stiffer.
The amount of weight an aluminum extrusion can hold is surprisingly high when you work with high-end materials. Why not take advantage and cut your assembly time by 50%?
Building With Aluminum Extrusion Frames – For Easy Modifications
Repurposability may not be your initial focus. Perhaps you’re building to a singular purpose.
However, one of the best use cases of extrusion building systems is future-proofing your setup for evolving needs. Three places to start include:
- Slots to spare
- Additional nuts
- Teardown
Open Slots
Do you want as many slots as possible on the assembly, or would the application benefit more from a nice aesthetic and clean edges?
If function is more important, consider spec’ing extra slots into your initial build. After all, you can’t add strengthening brackets if you lack the slots for them.
In highly aesthetic projects (and, occasionally, safety-minded ones), include only the necessary number of slots. This improves your modular framing’s long-term value in a few ways:
- With no visible edges, it’s easier to clean
- Dirt and debris won’t get into empty slots
- Workers can’t hang items from the frame or make unapproved adjustments
Additionally, you can use slot covers to help with #1 and #2.
Additional Nuts & Bolts
Repurposability is the most underused feature of aluminum modular framing. Repurposing a structure starts at the initial build.
Say you have a miter joint with a corner cut at 45°. Unfortunately, this design blocks the ends of profiles, so you can’t slide any extra components in from the sides.
Would you like to leave the ends of the profiles open so you can fit another feature on the frame? Well, what if you already have a bracket in place, but no nut there?
This might be the most common roadblock of building industrial modular structures with long-term value.
You end up taking the connection apart or using a straight nut (because you can’t use an angle nut). This solves the issue 90% of the time, but isn’t efficient.
Luckily, there are alternatives. Use a system that allows you to insert more connecting components if there’s a chance you’ll want to add to the structure later.
Drop-in T-nuts allow for easily adding components to a frame, however they are typically not as strong as a slide in T-nut. Some of them use a set screw or other methods to secure the nut in vertical or horizontal orientations to make installation easier. Drop-in T-studs use a similar concept. These threaded fasteners insert from the top of a slot on a framing profile.
Slide-in T-nuts have a larger surface area for heavy-duty support. However, you can only add them from the end of the profile.
Again, your design decisions here boil down to form vs. function. Do you want nice and clean, or the ability to easily adjust and add?
(Note: Access is also a consideration during repair. If a bolt can only go in one way, orient it that way.)
Teardown
The structure’s application and end-use environment may demand frequent teardown and setup. If that sounds like your industry, you absolutely should be building with disassembly and realignment in mind.
Historically, sturdier builds have been challenging to undo, then precisely recreate.
- Heavy, cumbersome welded steel would have to be cut out, and you may be stuck waiting on a skilled tradesperson to be available.
- T-slots are lightweight, but require a leveling square and lots of fussing to realign to original precision
This is another case where investing in a premium solution may offer the best total cost of ownership. Even though certain high-end aluminum framing doesn’t come loose during use, it’s still easy to disassemble. And no matter how many times you unbuild and rebuild it, you can realign it instantly.
Another consideration for on-the-move projects is clearance. Can you loosen the fastener all the way? Or will it make contact with the structure unless you disassemble other parts?
Every time you make a design decision that’s forward-thinking or simplifies the build, you recoup labor costs.
More Tips for a More Valuable Aluminum System
How do you design an aluminum extrusion frame so it helps, rather than harms, your operational efficiency? By thinking about the build – not just that first build, but also the ability to effortlessly adjust on the fly.
Building with aluminum extrusions for structural products can result in better:
- Precision
- Flexibility
- Durability
Just be sure your modular building materials match the rigors and required portability of your project.
For more resources on building modular structures with aluminum extrusions, see our blog hub:
Leave a Comment